技術情報
流動解析詳細
樹脂流動解析において、充填保圧解析と充填保圧反り解析は、射出成形工程における重要なシミュレーションです。
充填保圧解析
充填保圧解析は、樹脂が金型内にどのように流れ込むか(充填過程)と、その後の保圧段階(保持圧力をかけて樹脂の収縮を抑える)をシミュレーションする解析です。具体的には、以下のポイントに着目します。
- 充填解析:樹脂が射出され、金型内部のキャビティ(成形品の形状を決定する空間)にどのように充填されるかをシミュレーションします。樹脂の流れ方、流動速度、温度分布、圧力分布などから成形可否判断や成形条件の最適化を実施します。
- 保圧解析:充填が完了した後、樹脂が冷却され収縮するのを補正するために保圧をかける過程をシミュレーションします。ヒケやボイド、ショートショットの有無を確認します。
- 冷却解析:熱伝導と熱伝達による金型内での冷却挙動をシミュレーションします。金型表面温度や樹脂温度分布を計算し、冷却回路の配置や冷媒の温度を検討します。充填保圧解析との連成が可能です。
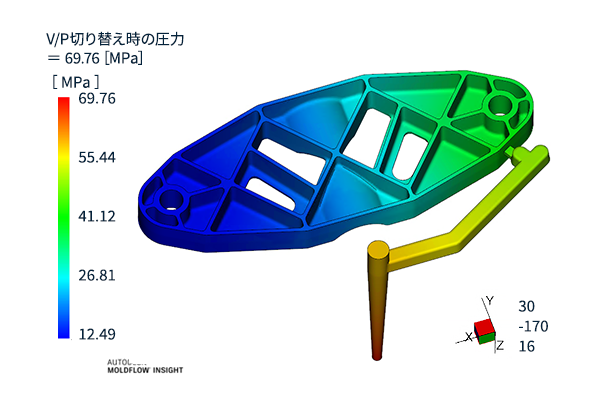
充填保圧反り解析
充填保圧反り解析は、上述の充填保圧解析に加えて、成形品が冷却される過程で発生する反りを解析するものです。射出成形後、樹脂が冷却・固化される際、収縮が不均一になることで生じる反りや変形をシミュレーションします。
- 反り解析:充填、保圧、冷却解析の結果を基に金型離型後の成形品の収縮・反り変形を予測します。冷却差・収縮差・配向差の3つの要因に反りの原因を分類でき、原因を特定してゲート位置の変更や成形条件の変更といった解決策を検討します。
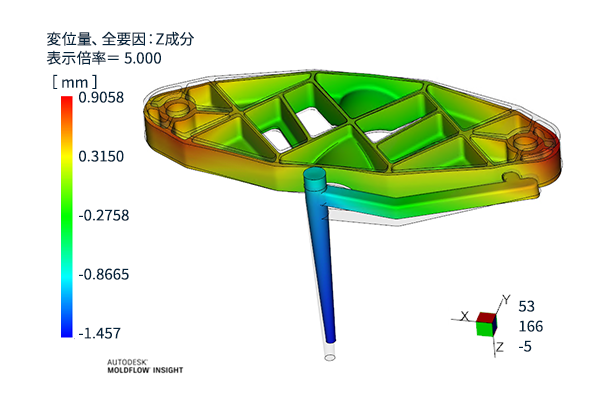
繊維配向の評価
ガラス繊維を含む繊維強化樹脂の場合は繊維配向が製品の性能に大きな影響を与える可能性があり、その配向を考慮することが重要です。
繊維配向情報を知るためには、流動解析で繊維配向テンソルの出力をします。
ここでは平板試験片を用いた評価の様子を示します(図4)。
繊維配向テンソルとは、繊維の方向の確率分布(0~1)のことです。ここでは、繊維配向テンソルをx軸方向、y軸方向、z軸方向の3軸で評価しています。テンソル値が大きくなる(1に近づく)につれ、各軸方向に繊維が揃っていることを意味します。
繊維配向テンソルの実測値は、評価位置の製品断面を光学顕微鏡などで観察し、その画像から独自の手法で算出しています。成形品の厚み方向に5%ごとに区切って繊維配向テンソルを算出しました。図4の拡大図の棒状や円形に写っているものがガラス繊維です。
図5に、繊維配向テンソルの実測値と流動解析から得られた解析値の結果を重ねて示しています。
解析により実際の繊維配向テンソルが予測できたといえます。
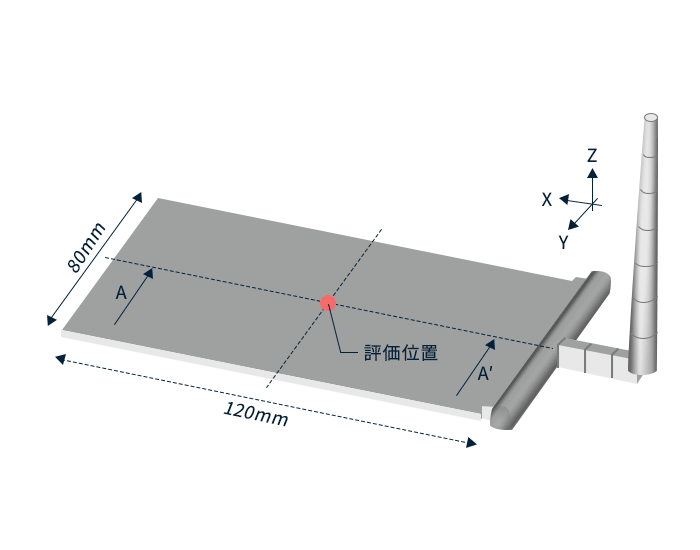
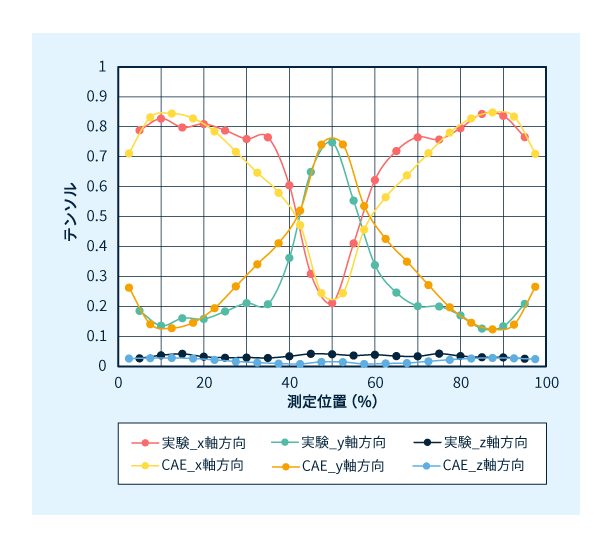