系列:塑料产品设计 CAE 分析基础
第 6 部分 如何使用注塑分析结果
我们将解释注塑分析的输出结果以及如何将获得的信息用于产品/模具设计和成型过程。
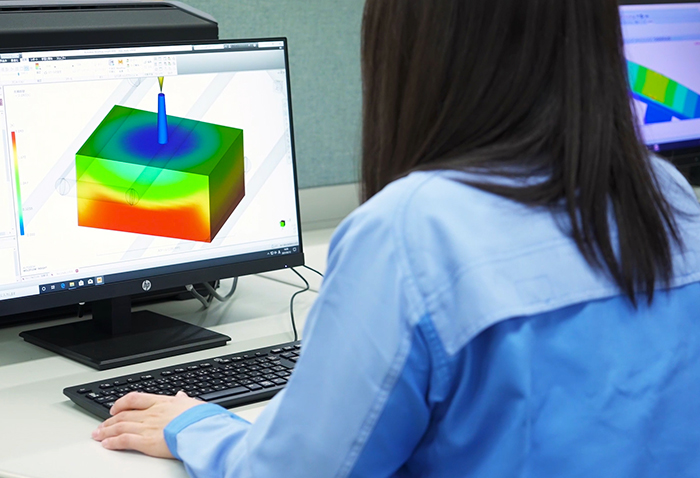
内容
1.首先 |
2. 注塑分析可以告诉我们什么? |
3. 分析结果将如何使用? |
4.一些常见的成型缺陷 |
5.总结 |
介绍
基于注塑分析的成型模拟的输出是什么?仿真结果通常以动画或等高线图的形式呈现,以便于视觉理解。本文介绍了输出信息的类型以及如何在设计和后续过程中利用它。
注塑分析可以告诉我们什么?
即使称为注塑成型分析,根据想要了解的内容,进行的分析也会有所不同。主要有四种分析:冷却分析、填充分析、保压分析、翘曲分析。
冷却分析是一种传热模拟,用于分析注塑模具中的热流。它用于确定填充树脂的型腔内部的温度、整个模具的温度以及冷却时间。
填充分析可预测填充过程中模具中树脂的流动。填充分析计算模腔中的流动前沿,该流动前沿从注射位置逐渐延伸,直到到达 V/P 切换位置。
保压分析可预测保压过程中模具中树脂的流动。通过按填充分析和保压分析的顺序执行,可以检查型腔是否完全被树脂填充。
翘曲分析可确定翘曲的原因并考虑解决方案,例如更改浇口位置、更改设计参数和减少壁厚变化。
从这些分析中可以获得以下输出信息。
■ 填充图案
填充图案是通过填充分析来验证树脂在成型品中的流动情况的结果。在网格模型中设置浇口位置、树脂类型和分析条件,可以验证树脂填充模式。如图 1 所示,梯度显示树脂如何通过浇口填充到模型中。
由于我们知道树脂填充的位置需要时间,因此我们可以在设计中反映这一点,例如,通过考虑适当的浇口位置或改变形状,例如难以流动的薄壁部分。
图1 填充图案示例
■ 填充完成时的树脂压力分布
填充分析可以可视化当型腔完全充满树脂时型腔内的压力如何分布。压力不均匀会导致成型品变形。此外,需要高压的产品可能会破坏模具。了解压力的施加位置和方式可用于模具设计。
图2 填充完成时树脂压力分布示例
■ 填充完成时的树脂温度分布
这是对模具完全充满树脂时树脂温度分布进行冷却和填充分析模拟的结果。树脂温度的变化会导致收缩不均匀并导致成型产品翘曲。该分析用于研究冷却效率和冷却水管道布置,以确保尽可能均匀的冷却。
图3 填充完成时树脂温度分布示例
■ 流动前沿温度
流动前沿是指注射到模具中的树脂流动的前缘,表示树脂到达成型品各部分的温度。它是在冷却分析中计算的。模具通常设置在比熔融树脂更低的温度,并且树脂的温度在填充过程中降低。如果在填充过程中流动前沿温度太低,可能会导致成型缺陷。
图4 流动前沿树脂温度示例
■ 模具表面温度分布
可以确认冷却后成型品表面(模具表面)的温度分布。通过检查模具固定侧和活动侧之间的冷却不均匀和温差是否较大,可以用来确定翘曲的原因。
图5 模具表面温度分布示例
■ 成型品各部分温度随时间的变化
冷却分析输出成型产品各部分随时间的温度变化。该分析检查可能导致变形和翘曲的热点和冷点等温度偏差,并检查浇口是否在成型产品之前凝固。还可以检查冷却是否均匀。
图6 成型品各部分温度随时间变化的例子
■ 成型品各部分的压力随时间的变化
整个成型产品的压力变化可以通过填充分析来分析。压力通常从 1 个大气压开始,并在达到流动前沿后增加。流动受限区域的压力增加,流动性因树脂类型而异。这样可以检查树脂流量是否足够,并且了解最大压力对于选择成型机尺寸很有用。
图7 成型品各部分的压力随时间变化的例子
■ 翘曲变形
翘曲分析利用冷却和填充分析的结果来预测成型产品的收缩和翘曲将如何发生。它还模拟将发生的变形程度。可以在产品设计阶段考虑和反映減小化翘曲的形状和浇口位置。
当产品收缩不均匀时就会发生翘曲变形。引起翘曲的主要原因有三个:冷却差异、收缩差异和方向差异,Moldlfow 通过打开“指定翘曲原因”选项来输出有关主要原因的信息。图8显示了所有因素的输出信息的结果。
图8 翘曲变形示例
■ V/P 切换时的压力
V/P切换是指当熔融树脂通过螺杆注射到模具中时,从注射过程(速度控制)到保压过程(压力控制)的转换。
V/P 切换时的压力指示速度控制填充过程中树脂的填充程度。在速度控制过程中,型腔不应完全充满树脂,未填充的区域通过压力控制完全重新填充。如果此时的保压压力太低,可能会产生缩痕,如果太高,可能会产生毛刺和模具破损。
通过填充分析来获得合适的成型条件。
图 9 V/P 切换时的压力示例
■ 注射位置压力
分析填充和保压过程中成型品各部分的压力随时间的变化。如果成型品的特定部位或多腔成型过程中成型品的某些部位压力不均匀,则可能会出现流动不平衡。检查流量问题和适当的压力保持。
图10 注射位置压力示例
■ 锁模力
锁模力是填充树脂时保持模具紧密所需的力的大小。适当的值是从整个成型产品的压力分布获得的。根据成型所需的锁模力,需要选择合适尺寸的成型机。
图11 锁模力示例
■ 纤维取向张量
在含有玻璃纤维的树脂中,纤维取向会导致一些方向收缩不均匀和强度弱等问题。对于纤维增强树脂,可以使用纤维取向分析来确定成型过程完成后的纤维取向和取向张量(取向度)。为了利用纤维增强树脂的特性,提前了解取向趋势非常重要。
图12 纤维取向张量示例
■ 缩痕估计
根据填充分析和保压分析,我们可以预测成型产品中可能出现缩痕的位置及其深度。打嗝通常发生在成型产品厚壁、加强筋、凸台和内部圆角的另一侧。通过分析形状、浇口位置、模具和树脂温度降低等不同成型条件,可以找出缩痕的原因并采取对策。
图13 缩痕预测示例
■ 熔接线估计
填充分析可预测熔接线将出现的位置。熔接线出现在树脂与树脂相遇的地方。由于熔接线会导致强度不足和外观缺陷,因此可以通过将浇口位置调整到从外部不太可见的位置,或通过调节相遇角度(树脂与树脂碰撞的角度)来使熔接线变得不那么明显。
图 14 熔接线预测示例
分析结果将如何使用?
我们将解释如何将从注塑分析中获得的信息应用于产品/模具设计和成型工艺。在需要判断的情况下,可以利用分析数据得出合理、客观的指标。
■ 所需成型机尺寸
为了知道合适的成型机尺寸,重要的是要知道合适的锁模力、注射压力等的大小。通过使用注射成型分析,可以知道这些值并可以提前考虑成型机的尺寸。成型机的尺寸直接关系到成型进度和成本,因此有必要进行生产规划。
■ 流动性的确定
根据填充模式、压力、树脂温度等因素,检查成型品是否能够填充树脂,无过量或不足。我们通过提前研究和采取对策,例如调整薄壁区域或难以流动的流道或改变树脂类型,为减少成型阶段的问题做出贡献。
■ 浇口位置优化
根据填充形状、熔接等,确认哪个浇口位置有利于成型,并能防止发生缺陷。此外,确认改变浇口位置是否会引起其他问题,并通过优先顺序判断来确定适当和理想的位置也很重要。
■ 成型条件的优化
适当和理想的成型条件取决于 V/P 切换压力、注射位置、模具温度和冷却速度。设定成型条件需要经验和知识,因此通常由成型工程师负责。
■ 模具冷却优化
根据模具温度分布和温度随时间的变化情况,调整水管位置和冷却水温度,尽可能均匀地冷却模具。适当的冷却很重要,因为冷却不足或不均匀可能会导致成型缺陷。如果生产开始后出现成型问题,则很难对模具进行重大改动,例如更换水管,因此必须提前充分考虑并采取对策。
■ 通过上述优化改善翘曲变形
压力不均匀、冷却不均匀、纤维取向等都会引起成型品的翘曲,特别是对尺寸精度要求严格的产品,可以尽量通过注塑成型分析提前进行验证,并采取对策,将变形量降到低。
一些常见的成型缺陷
注塑分析可用于预测可能的成型缺陷和故障。成型缺陷是批量生产成型中不可避免的问题,注塑分析可以帮助地减少其发生。下面列出了一些常见的成型缺陷。
■ 短镜头
短射是指熔融树脂未完全充满模具尖端的成型缺陷。存在短射的成型品无法回收。短射是由于树脂流量不足、注射压力不足或保压压力不足造成的。通过调节V/P切换压力位置、注射压力和浇口位置来控制发生。
图 15 短射示例
■ 熔接线
填充到成型产品中的熔融树脂的汇合处可能会形成一条细的划痕状线,称为熔接线。这些焊缝很脆弱,在强度测试过程中可能会被损坏。它们也可能看起来像外部的划痕,这可能会导致消费者投诉。对策包括改变浇口位置以使熔接线不会出现在突出区域、调整模具温度以及调整成型产品的厚度以控制两个熔体前沿之间的相遇角度。 。
图 16 熔接线示例
■ 烧痕
烧痕是成型品的一部分燃烧、变黑、碳化的现象。当熔融树脂在高压下注射时,会发生这种情况,导致型腔中的空气失去其位置并被压缩,从而产生高热。烧痕往往不是在成型初期出现,而是在大批量生产时出现,成型过程中常常因需要防止烧痕而受到困扰。除了降低注射速度外,设置排气口以释放气体并通过改变浇口位置和壁厚来控制树脂流动也是有效的。
图 17 烧伤痕迹示例
■ 缩痕
缩痕是一种外观缺陷,是由于成型品不同部位的收缩率差异(例如壁厚不同)造成的。这可以通过调整浇口位置、增加注射压力、冷却效率和调整壁厚来解决。由于这种缺陷往往发生在肋和凸台等较厚的部分,因此在设计阶段采取对策非常重要。
图 18 缩痕示例
概括
在产品设计和模具设计阶段,对成型过程中可能出现的问题进行模拟并采取对策非常重要。为此,设计师还需要了解成型知识。考虑到可塑性进行设计将减少返工并直接缩短开发时间。并非所有成型问题都可以仅通过成型过程来消除。有必要从设计阶段就采取对策,学会如何使用CAE仿真结果,并在设计中充分利用它们。
下一篇:《成型缺陷预测》
有关CAE的更多信息,请联系我们。