- SPITZE
- 技術サポート
- CAE-Fallstudien
- Genauigkeitsvalidierung der Auswirkungsanalyse: Ölwanne
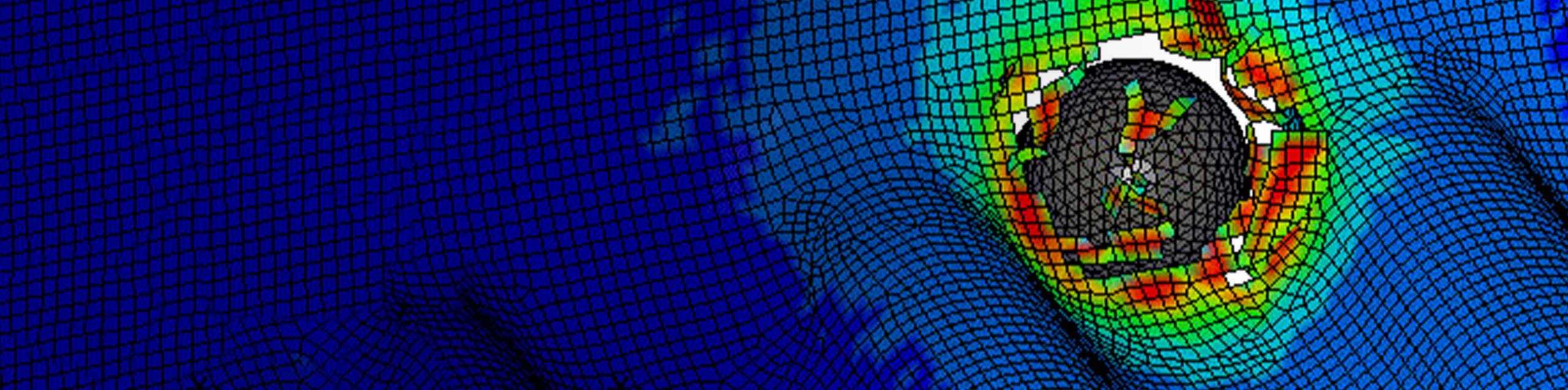
Fallstudie: Auswirkungsanalyse
Genauigkeitsvalidierung der Auswirkungsanalyse: Ölwanne
Zusammenfassung
- Wir haben die Leistung einer Kunststoff-Ölwanne validiert, deren Gewicht durch Topologieoptimierung im Vergleich zum ursprünglichen Metallteil um 60 % reduziert wurde.
- オイルパンは車体下部にありチッピングという現象が生じやすいため、チッピングを想定した実験や解析をすることで、強度の評価をします。
- Es wurde eine Simulation des Aufpralls einer Metallkugel auf eine Kunststoff-Ölwanne durchgeführt und mit einem tatsächlichen Test unter Verwendung einer Hochgeschwindigkeitskamera validiert. Beide Ergebnisse waren vergleichbar und wiesen ein hohes Maß an Genauigkeit auf.
Einführung
Die Reduzierung des Fahrzeuggewichts ist für die Reduzierung der CO 2-Emissionen von entscheidender Bedeutung, da sie direkte Auswirkungen auf den Kraftstoffverbrauch hat.
Wir haben die Leistung einer Kunststoff
-Ölwanne bewertet, deren Gewicht durch Topologieoptimierung im Vergleich zum ursprünglichen Metallteil um 60 % reduziert wurde.
Die Ölwanne befindet sich unten an der Fahrzeugkarosserie und ist anfällig für Schäden durch Steinschlag.
Wir haben experimentelle und analytische Ergebnisse zum Steinschlag verglichen.
Die Reduzierung des Fahrzeuggewichts ist für die Reduzierung der CO 2-Emissionen von entscheidender Bedeutung, da sie direkte Auswirkungen auf den Kraftstoffverbrauch hat.
Wir haben die Leistung einer Kunststoff-Ölwanne bewertet, deren Gewicht durch Topologieoptimierung im Vergleich zum ursprünglichen Metallteil um 60 % reduziert wurde.
Die Ölwanne befindet sich unten an der Fahrzeugkarosserie und ist anfällig für Schäden durch Steinschlag.
Wir haben experimentelle und analytische Ergebnisse zum Steinschlag verglichen.
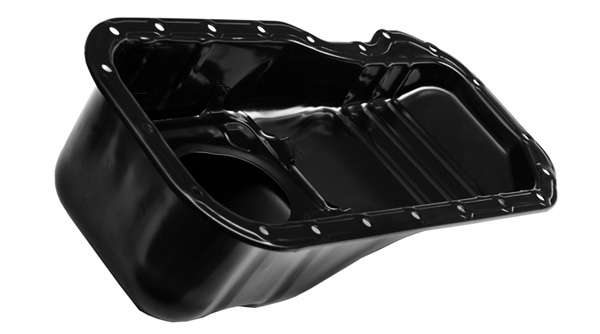
Abb.1 Ölwanne
Zweck
Vergleich experimenteller und analytischer Ergebnisse beim Steinschlag
Methoden
Die Auswirkungsanalyse wurde mit LS DYNA (Livermore Software Technology) durchgeführt.
Die Absplitterungsbedingungen wurden so definiert, dass eine Metallkugel, die einen Stein nachahmt, mit 80 km/h auf eine Kunststoff-Ölwanne aufprallt. Die Analyseergebnisse wurden mithilfe einer Hochgeschwindigkeitskamera mit dem tatsächlichen Test verglichen.
Bei der Auswirkungsanalyse ist es wichtig, die richtigen Randbedingungen für die Befestigung des Produkts festzulegen.
Da die Ölwanne um den Flansch herum verschraubt ist, wurden die Schraubenlöcher in der Analyse vollständig eingeschränkt (Abb. 2).
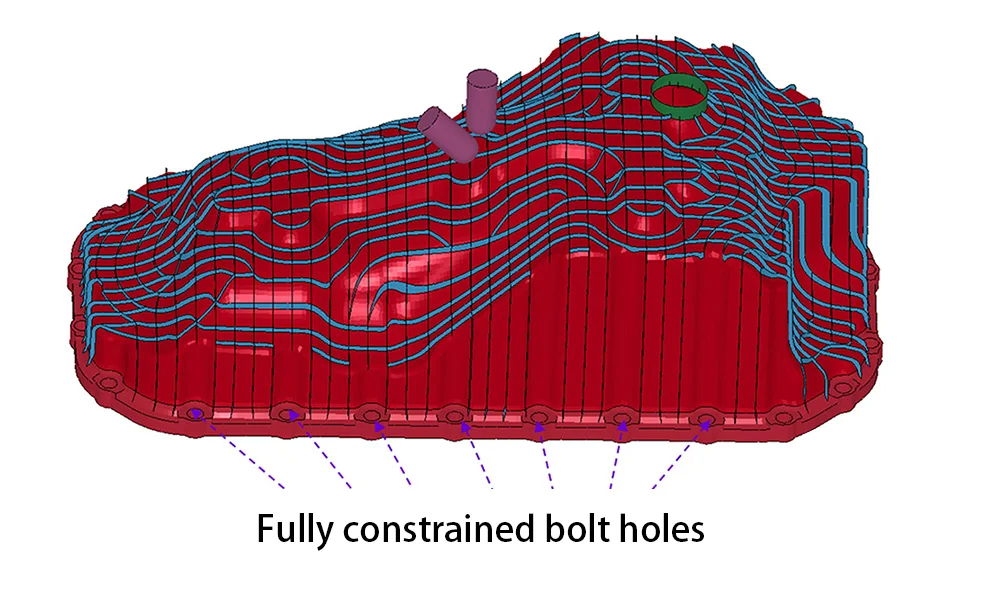
Abb.2 Randbedingung
Ergebnisse
Vergleicht man das Video in Abb. 3, so stimmen die Simulation und die tatsächlichen Versuchsergebnisse gut überein.
Auch bei der Anwendung auf reale Produkte, bei denen es sich nicht um Testexemplare handelt, konnten wir die Ergebnisse mit einem hohen Grad an Genauigkeit vorhersagen.
Einer der Gründe für die hohe Genauigkeit der Vorhersage ist, dass wir nach der Spritzgussanalyse ein Deformationsmodell nach dem Verzug verwendet haben.
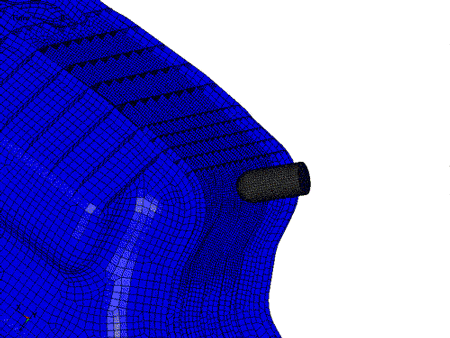
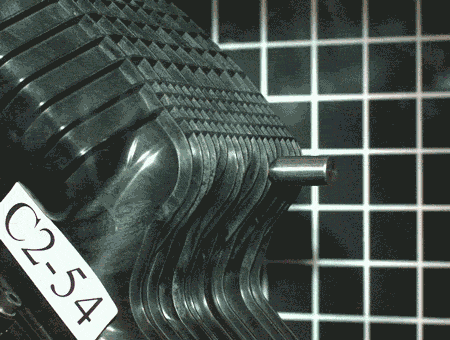
Abb. 3 Vergleich der Simulation und der tatsächlichen Versuchsergebnisse
Materialmodell
In dieser Analyse wird LEONA TM 14G33 (PA66, GF33%) verwendet.
LEONA TM 14G33 ist ein kristallines Harz aus der Gruppe der Thermoplaste.
Kristallines Harz bildet durch langsames Abkühlen aus dem geschmolzenen Zustand Sphärolithe. Die Sphärolithe enthalten eine Mischung aus lamellaren kristallinen Anteilen mit gefalteten Molekülketten von etwa 10 nm Größe und amorphen Anteilen mit zufällig gewundenen Molekülketten.
Beim Verformungsprozess kristalliner Harze wird mit fortschreitender Verformung die Bildung von Haarrissen beobachtet, eine für Harze typische mikroskopische Beschädigung.
Als diese Analyse durchgeführt wurde, gab es nur wenige Materialmodelle für die Aufprallanalyse von Harzmaterialien. Einige der Simulationen wurden sogar mit Materialmodellen für Metallmaterialien durchgeführt.
Aus diesem Grund haben wir ein neues ursprüngliches Materialmodell für kristalline Polymere entwickelt, das auf dem Haarrißverhalten basiert (Abb. 4).
Bei Interesse an den im Werkstoffmodell verwendeten Gleichungen wird auf die entsprechende Literatur verwiesen.
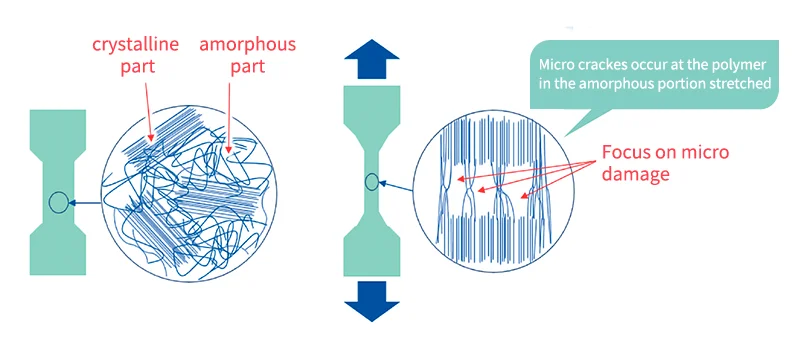
Abb. 4 Materialmodell unter Berücksichtigung des Craze-Effektes
Für weitere Informationen zu CAE kontaktieren Sie uns bitte.
Rückfragen