- SPITZE
- Grundlagen der CAE
- Teil 4 Was ist Spritzguss?
Serie: Grundlagen der CAE-Analyse für das Kunststoffproduktdesign
Teil 4 Was ist Spritzguss?
Vom 4. bis zum 9. werden wir stufenweise die Spritzgusssimulation von den zu verwendenden Materialdaten bis hin zu den spezifischen Anwendungsinhalten wie Gegenmaßnahmen gegen Formfehler vorstellen.
In diesem Artikel konzentrieren wir uns auf das Spritzgießen.
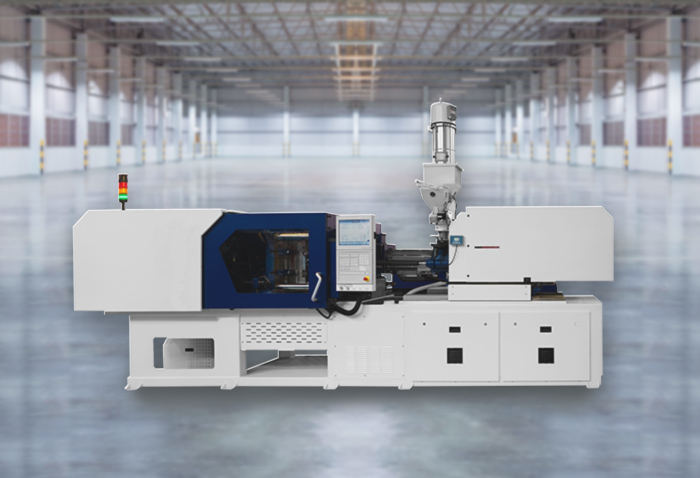
Inhalt
1. Was ist Spritzguss? |
2. Aufbau der Form für Spritzguss |
3. Spezielle Spritzgussverfahren |
4. Andere wichtige Formverfahren |
5. Zusammenfassung |
Was ist Spritzguss?
Spritzguss ist ein Verfahren, um Thermoplaste in die gewünschte Form zu bringen. Kunststoffe werden durch Erhitzen geschmolzen, unter Druck in eine Form gespritzt und gekühlt, um das Harz zu verfestigen.
Es ist möglich, komplexe Formen zu formen, wodurch die Herstellung einer großen Produktvielfalt möglich wird. Darüber hinaus ist es aufgrund der kurzen Formzeit pro Teil und der einfachen Automatisierung des gesamten Prozesses für die Massenproduktion geeignet.
Abb. 1 Beispiel einer horizontalen Spritzgussmaschine
Eine Spritzgussmaschine besteht aus einer Spritzeinheit und einer Formschließeinheit. Zunächst werden in der Spritzeinheit körnige Kunststoffrohstoffe (Pellets) aus dem Trichter zugeführt und durch Erhitzen im Zylinder geschmolzen. Das geschmolzene Harz wird unter hohem Druck mit einer Schnecke extrudiert und durch eine Düse in die Form eingespritzt. In der Formschließeinheit wird die Form nach dem Schließen und Einspritzen des Harzes abgekühlt und ausgehärtet. Öffnen Sie dann die Form und entnehmen Sie das geformte Produkt. Der Spritzgusszyklus besteht aus Formschließen → Einspritzen → Nachdruck → Abkühlen → Formöffnen → Auswerfen. Nachdruck ist ein Vorgang, bei dem sich das Harz bei Erhitzung ausdehnt und bei Abkühlung zusammenzieht, sodass die Schrumpfung durch Anwenden von Druck und weiteres Zuführen des Harzes ausgeglichen wird.
Aufbau einer Form für das Spritzgießen
Die Form für den Spritzguss hat die Form einer Taiyaki-Form. Die Seite, die sich beim Öffnen der Form öffnet, wird als bewegliche Seite (Kern) bezeichnet, und die Seite, die sich nicht bewegt, wird als feste Seite (Hohlraum) bezeichnet.
Abb. 2 Bewegung beim Öffnen und Schließen der Form
Der Anguss ist der Teil, der aus der Düse der Spritzgussmaschine gespritzt wird, wenn man das aus der Form genommene Formprodukt betrachtet. Er hat eine konische Form, sodass er leicht aus der Form entfernt werden kann. Geschmolzenes Harz fließt vom Anguss durch einen Fließkanal, der als Anguss bezeichnet wird, und fließt in das Produkt. Die Grenze zwischen Anguss und Produkt wird als Anguss bezeichnet und je nach Produkt werden verschiedene Formen ausgewählt. Kunststoffmodelle werden mit den am Anguss befestigten Teilen verkauft, aber bei normalen Produkten sind die Anguss- und Angussteile unnötig und müssen entfernt werden. Auch die Naht zwischen der festen Seite und der Bedienseite wird als Teillinie (PL) bezeichnet.
Abb. 3 Anguss, Angusskanal und Anschnitt des geformten Produkts
■ Zwei-Platten-Form
Eine Form, die aus einer festen und einer beweglichen Seite besteht. Da die Anzahl der Teile klein und einfach ist, können die Kosten der Form niedrig gehalten werden. Da das geformte Produkt jedoch mit noch angebrachten Angüssen und Läufern ausgetragen wird, ist eine Nachbehandlung namens Angussschneiden (Laufkantenbehandlung) erforderlich, um diese zu entfernen.
Abb. 4 Zweiplatten-Formbild
■ Drei-Platten-Form
Diese Form besteht aus drei Teilen: der festen Seite, der beweglichen Seite und der Angussabstreifplatte. Da Anguss und Angusskanal beim Öffnen der Form vom Produkt entfernt werden, eignet sie sich für die Automatisierung.
Abb. 5 Dreiplattenformbild
■ Heißkanalform
Dabei handelt es sich um eine Form, die die Anguss- und Angussteile mit einem Heizgerät erhitzt und nur das Auswerfen des Produktteils ermöglicht. Dadurch entfällt nicht nur die Notwendigkeit, Anguss- und Angussteile nach dem Formen zu bearbeiten, sondern es wird auch der Abfall von Kunststoffrohstoffen reduziert, sodass sich die Form für Automatisierung und Massenproduktion eignet. Die Formkosten sind hoch, da die Formstruktur kompliziert ist, einschließlich der eingebauten Heizung, die den Anguss erhitzt.
Abb. 6 Heißkanal-Werkzeugbild
■ Tortyp
Es gibt verschiedene Angussformen. Je nach Produktform, Anwendung, Formverfahren usw. muss die am besten geeignete Form ausgewählt werden. Hier stellen wir einige typische Typen vor.
・Direktes Tor
Abb. 7 Beispiel für Direktgate
Bei dieser Methode fließt das Material direkt vom Anguss in das Formprodukt, ohne durch einen Angusskanal zu gehen. Geeignet für große Formprodukte, aber es ist eine Nachbearbeitung erforderlich, da große Angussstellen verbleiben. Wird häufig zum Formen von Dingen wie Eimern verwendet.
・Seitentor
Abb. 8 Seitentor-Beispiel
Dies ist eine Methode, um ein Tor an der Seite des Produkts anzubringen. Sie wird häufig verwendet, da mehrere geformte Produkte erhältlich sind und die Verarbeitung einfach ist. Da eine Nachbearbeitung erforderlich ist und Torspuren verbleiben, muss über die Installation des Tors an einer unauffälligen Stelle nachgedacht werden.
・Filmtor
Abb. 9 Beispiel für ein Filmfenster
Bei dieser Methode wird ein dünner, filmartiger, länglicher Anguss entlang des Formprodukts angebracht. Da der Anguss breit ist und das Harz gleichmäßig fließt, eignet sich diese Methode für dünne, plattenförmige Formprodukte, die zu Verformungen und Verzerrungen neigen. Sie wird auch verwendet, um Formfehler aufgrund der Ausrichtung von Harzen zu verhindern, die Füllstoffe wie Verstärkungsfasern enthalten. Da der Anguss dünn und breit ist, ist es schwierig, die Angussspuren zu entfernen, und es ist eine Nachbearbeitung erforderlich.
・Pin-Gate
Abb. 10 Beispiel für ein Pin-Gate
Angussöffnungen, die in Dreiplattenformen verwendet werden. Geeignet für die Automatisierung, da die Angussöffnung abbricht, wenn die Form geöffnet wird und sich das Teil vom Angusskanal löst. Sie können mehrere Angussöffnungen setzen oder mehrere Teile verwenden. In diesem Fall ist es notwendig, das Gleichgewicht zu berücksichtigen und die Position zu bestimmen, damit das Harz gleichzeitig in jedes geformte Produkt gegossen werden kann. Da die Angussöffnung kleiner gemacht werden muss, kann es bei Harzen mit geringer Fließfähigkeit oder Füllstoffen schwierig sein.
・U-Boot-Tor
Abb. 11 Beispiel eines Unterwassertors
Dies ähnelt dem Seitenanguss, aber dies ist eine Methode, bei der das Harz so gegossen wird, als würde es unter das Produkt kriechen. Wird auch Tunnelanguss genannt. Es ist keine Nachbearbeitung erforderlich, da der Anguss beim Öffnen der Form bricht. Wie bei Stiftanguss kann es bei Harzen mit geringer Fließfähigkeit oder gefüllten Harzen schwierig sein.
Spezielles Spritzgussverfahren
Derzeit werden verschiedene spezielle Formverfahren entwickelt, um Probleme beim Spritzgießen zu lösen und die Qualität zu verbessern. Hier sind einige repräsentative Beispiele.
■ Gaseinspritzung
Gasinjektion (gasunterstütztes Formen) ist ein Haltedruckverfahren, bei dem Druck ausgeübt wird, bis das Produkt abgekühlt und verfestigt ist, nachdem es im normalen Spritzgussverfahren mit Harz gefüllt wurde. Einfallstellen (Beulen, die auf der Oberfläche entstehen, wenn das Harz abkühlt und schrumpft) und Verformungen von geformten Produkten können unterdrückt werden, wodurch die Maßgenauigkeit verbessert wird.
■ Überkritisches Schäumen
Wenn Stickstoff oder Kohlendioxid hohen Temperaturen und Drücken ausgesetzt werden, entsteht ein Zustand, in dem sowohl Gas als auch Flüssigkeit vorhanden sind. Eine Substanz in diesem Zustand wird als überkritisches Fluid bezeichnet. Dies ist ein Formverfahren, bei dem ein überkritisches Fluid als Treibmittel in ein Harz eingespritzt und geschmolzen wird. Anschließend werden abrupte Druck- und Temperaturänderungen angewendet, um mikroskopische Schäume zu erzeugen. Dadurch wird das Innere des Formprodukts zu einer mikrozellulären Struktur. Es ist zu erwarten, dass das Gewicht der Formprodukte reduziert wird. Da außerdem die Fließfähigkeit verbessert wird, ist es möglich, die Wand dünner zu machen und die verwendete Harzmenge zu reduzieren. Darüber hinaus wird durch die Erzeugung gleichmäßiger Luftblasen im Inneren des Harzes ein gleichmäßiger Druck ausgeübt, wodurch Verformungen und Einfallstellen vermieden und die Maßgenauigkeit verbessert werden können. Es reduziert die Formschließkraft der Formmaschine und macht den Haltedruck überflüssig, wodurch der Formzyklus verkürzt werden kann.
■ Heizen und Kühlen
Wenn geschmolzenes Harz in eine Form gefüllt wird und die Formtemperatur niedrig ist, kühlt das Harz schnell ab und härtet an den Stellen aus, an denen es aufliegt, was zu optischen Mängeln wie Schweißnähten (Rillen, die sich dort bilden, wo das Harz in die Form eindringt) führt. Daher wird das Innere der Form mit einem Heizgerät oder einem anderen Gerät erhitzt, um sicherzustellen, dass das Harz die optimale Temperatur hat, um die Form der Form zu übertragen. Darüber hinaus kann diese Methode durch schnelles Abkühlen der Form zum Aushärten des Harzes die optische Qualität des geformten Produkts verbessern, beispielsweise durch die Beseitigung von Schweißnähten und Fließspuren.
Andere wichtige Formverfahren
Neben dem Spritzguss gibt es viele weitere Formen für Thermoplaste. Einige der wichtigsten Formen werden im Folgenden kurz beschrieben.
■ Extrusionsformen
Dieses Formverfahren eignet sich zur Herstellung röhrenförmiger Produkte wie Schläuche und Strohhalme sowie langer Produkte mit einheitlichem Querschnitt wie Schienen und Fensterflügel. Das Formen erfolgt durch Extrudieren von erhitztem und geschmolzenem Harz aus einer Form (Matrize) mit einem Querschnittsloch. Das extrudierte Harz wird zum Aushärten mit Wasser oder Luft gekühlt. Abhängig von der Form der Matrize ist es möglich, kontinuierlich Rohre mit verschiedenen Querschnittsformen zu formen.
■ Blasformen
Dieses Formverfahren eignet sich zum Formen von Hohlformen wie PET-Flaschen. Das geschmolzene Harz wird in eine zylindrische Form extrudiert, in eine Form gegeben und durch Einblasen von Hochdruckluft aus der Öffnung wie ein Ballon aufgeblasen. Es wird geformt, indem das Harz von innen mit der Kraft der Luft gegen die Form gedrückt und zum Anhaften gebracht wird. Nicht zum Formen komplexer Formen geeignet.
■ Vakuumformen
Dies ist eine Methode zum Formen von Eierkartons, Verpackungen für verschiedene Waren und Lebensmittel. Eine Harzplatte wird erhitzt, erweicht, in eine Form gelegt und Luft abgesaugt, um ein Vakuum zu erzeugen. Anschließend wird die Harzplatte zum Formen an die Form geklebt. Für die Formen können andere Materialien als Metall verwendet werden, wie Gips und Holz, die leicht zu verarbeiten sind und relativ kostengünstig geformt werden können. Obwohl es möglich ist, große Objekte wie Autoarmaturenbretter, Stoßstangen und Badewannen zu formen, ist es nicht zum Formen präziser und komplizierter Formen geeignet.
Zusammenfassung
Bei der Massenproduktion von Kunststoffprodukten ist es notwendig, die Grundlagen der Formstruktur und des Spritzgusses zu kennen. Dies liegt daran, dass Formen und Angussformen ausgewählt werden müssen, die der Anwendung und den Eigenschaften des Produkts entsprechen. In der Spritzgusssimulation können Sie den gesamten Spritzgussprozess simulieren und die Defektphänomene beim tatsächlichen Spritzguss überprüfen, was für die Gestaltung der Form und die Festlegung der Spritzgussbedingungen nützlich sein kann. Im nächsten Teil erklären wir ausführlich, wie es verwendet werden kann.
Nächster Teil: „Erfahren Sie mehr über Materialdatenelemente, die für die Spritzgusssimulation verwendet werden.“
Für weitere Informationen zu CAE kontaktieren Sie uns bitte.
CAE-Download-Folien
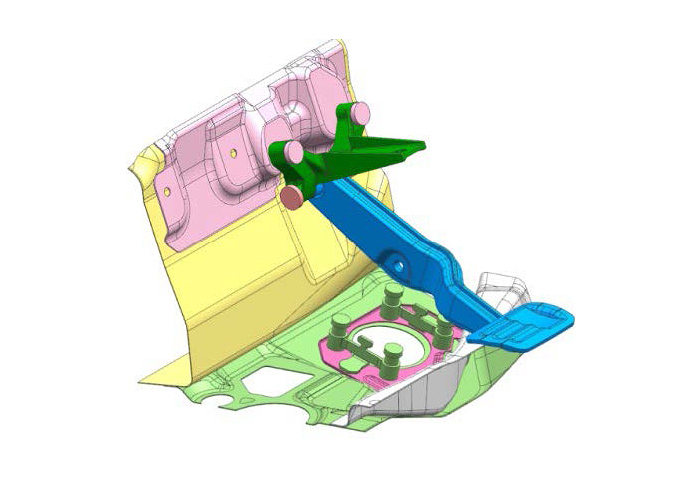
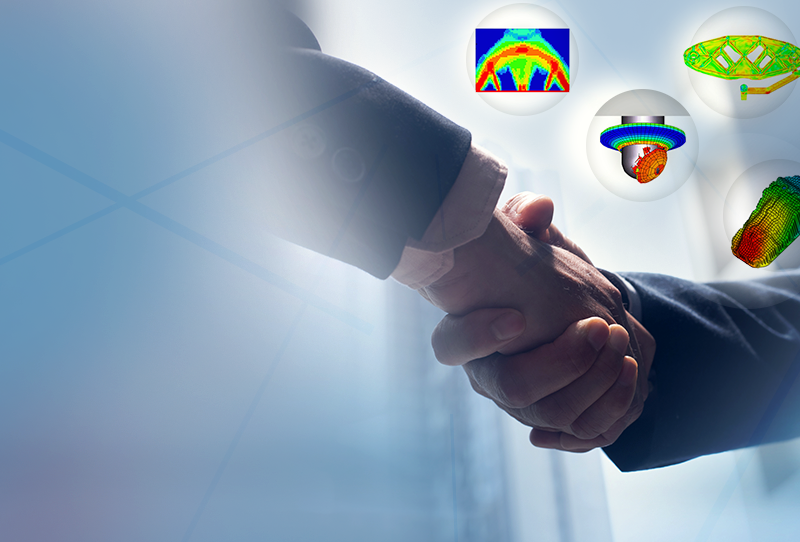