- SPITZE
- Grundlagen der CAE
- Teil 6: So nutzen Sie die Ergebnisse der Spritzgussanalyse
Serie: Grundlagen der CAE-Analyse für das Kunststoffproduktdesign
Teil 6 So verwenden Sie die Ergebnisse der Spritzgussanalyse
Wir erläutern die Ergebnisse der Spritzgussanalyse und wie die erhaltenen Informationen beim Produkt-/Formdesign und im Formprozess genutzt werden können.
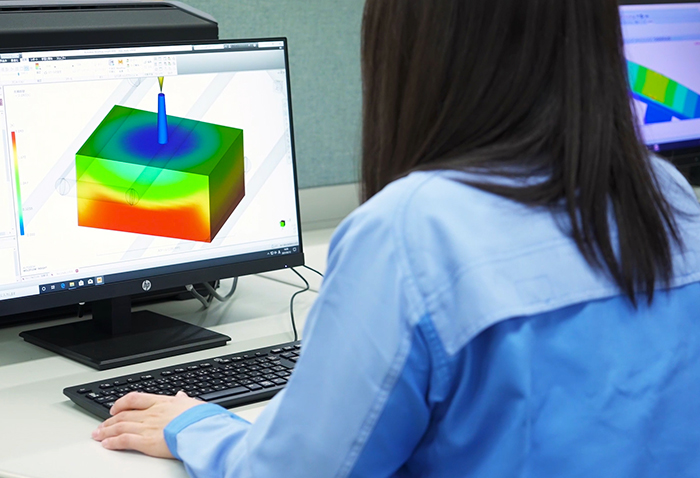
Inhalt
1. Einleitung |
2. Was kann uns eine Spritzgussanalyse sagen? |
3. Wie werden die Analyseergebnisse genutzt? |
4. Einige der häufigsten Formfehler |
5. Zusammenfassung |
Einführung
Was ist das Ergebnis einer Formsimulation basierend auf einer Spritzgussanalyse? Simulationsergebnisse werden im Allgemeinen als Animationen oder Konturdiagramme dargestellt, um ein einfaches visuelles Verständnis zu ermöglichen. Dieser Artikel stellt die Arten von Ausgabeinformationen vor und erläutert, wie diese im Design und in nachfolgenden Prozessen verwendet werden.
Was kann uns eine Spritzgussanalyse sagen?
Auch wenn es Spritzgussanalyse heißt, unterscheidet sich die durchzuführende Analyse je nachdem, was Sie wissen möchten. Es gibt vier Hauptanalysen: Kühlanalyse, Füllanalyse, Nachdruckanalyse und Verzugsanalyse.
Die Abkühlungsanalyse ist eine Wärmeübertragungssimulation, die zur Analyse des Wärmeflusses in einer Spritzgussform verwendet wird. Sie wird verwendet, um die Temperatur innerhalb des mit Harz gefüllten Hohlraums, die Temperatur der gesamten Form und die Abkühlungszeit zu bestimmen.
Die
Füllanalyse sagt den Harzfluss in der Form während des Füllvorgangs voraus. Die Füllanalyse berechnet die Fließfront im Formhohlraum, die sich schrittweise von der Einspritzposition bis zum Erreichen der V/P-Umschaltposition ausdehnt.
Die Packanalyse sagt den Harzfluss in der Form während des Packvorgangs voraus. Durch Ausführen der Füllanalyse und der Druckhalteanalyse in der Reihenfolge kann überprüft werden, ob der Hohlraum vollständig mit Harz gefüllt ist.
Durch die Verzugsanalyse werden die Ursachen des Verzugs ermittelt und Lösungsansätze wie die Änderung der Angusspositionen, die Änderung der Konstruktionsparameter und die Reduzierung von Wanddickenschwankungen in Betracht gezogen.
Aus diesen Analysen können folgende Ausgabeinformationen gewonnen werden.
■ Füllmuster
Ein Füllmuster ist das Ergebnis der Überprüfung des Harzflusses in einem geformten Produkt durch Füllanalyse. Die Angussposition, der Harztyp und die Analysebedingungen werden im Netzmodell festgelegt, und das Harzfüllmuster kann überprüft werden. Wie in Abbildung 1 dargestellt, zeigt der Farbverlauf, wie das Harz durch den Anguss in das Modell gefüllt wird.
Da wir wissen, wo das Füllen des Harzes Zeit in Anspruch nimmt, können wir dies im Design berücksichtigen, indem wir zum Beispiel geeignete Angussstellen berücksichtigen oder Formen ändern, wie etwa dünnwandige Abschnitte, deren Fließen schwierig ist.
Abb. 1 Füllmusterbeispiel
■ Harzdruckverteilung bei Füllende
Die Füllanalyse kann visualisieren, wie sich der Druck im Hohlraum verteilt, wenn dieser vollständig mit Harz gefüllt ist. Ungleichmäßiger Druck kann zu Verformungen des geformten Produkts führen. Darüber hinaus können Produkte, die hohen Druck erfordern, die Form zerstören. Wenn man weiß, wo und wie Druck ausgeübt wird, kann man das bei der Formgestaltung nutzen.
Abb. 2 Beispiel der Harzdruckverteilung bei Füllende
■ Harztemperaturverteilung bei Füllende
Dies ist das Ergebnis einer Kühl- und Füllanalyse-Simulation, die zeigt, wie sich die Harztemperatur verteilt, wenn die Form vollständig mit Harz gefüllt ist. Schwankungen der Harztemperatur können zu ungleichmäßiger Schrumpfung und Verformung des geformten Produkts führen. Diese Analyse dient der Untersuchung der Kühleffizienz und der Anordnung der Kühlwasserrohre, um eine möglichst gleichmäßige Kühlung zu gewährleisten.
Abb. 3 Beispiel der Harztemperaturverteilung bei Füllende
■ Temperatur an der Fließfront
Die Fließfront bezeichnet die Vorderkante des in die Form eingespritzten Harzflusses und gibt die Temperatur an, bei der das Harz jeden Teil des geformten Produkts erreicht. Sie wird in einer Abkühlungsanalyse berechnet. Die Form wird häufig auf eine niedrigere Temperatur als das geschmolzene Harz eingestellt, und die Temperatur des Harzes sinkt während des Füllvorgangs. Wenn die Fließfronttemperatur während des Füllvorgangs zu niedrig ist, können Formfehler auftreten.
Abb. 4 Beispiel der Harztemperatur an der Fließfront
■ Temperaturverteilung an der Werkzeugoberfläche
Die Temperaturverteilung auf der Oberfläche des geformten Produkts (Formoberfläche) nach dem Abkühlen kann bestätigt werden. Dies kann verwendet werden, um die Ursache des Verzugs zu ermitteln, indem auf ungleichmäßige Abkühlung und große Temperaturunterschiede zwischen der festen und der beweglichen Seite der Form geprüft wird.
Abb. 5 Beispiel für die Temperaturverteilung an der Werkzeugoberfläche
■ Zeitliche Schwankung der Temperatur jedes Teils des geformten Produkts
Die Temperaturschwankungen jedes Teils des geformten Produkts im Laufe der Zeit werden aus der Abkühlungsanalyse ausgegeben. Diese Analyse prüft auf Temperaturabweichungen wie heiße und kalte Stellen, die zu Verformungen und Verwerfungen führen können, und prüft auch, ob das Tor vor dem geformten Produkt erstarrt. Es ist auch möglich, auf gleichmäßige Abkühlung zu prüfen.
Abb. 6 Beispiel für die zeitliche Veränderung der Temperatur jedes Teils eines Formprodukts
■ Zeitliche Druckschwankungen in den einzelnen Teilen des Formprodukts
Die Druckschwankungen im gesamten Formprodukt können durch Füllanalyse analysiert werden. Der Druck beginnt normalerweise bei 1 atm und steigt an, sobald die Fließfront erreicht ist. Der Druck steigt in Bereichen mit eingeschränktem Durchfluss und die Fließfähigkeit ist je nach Harztyp unterschiedlich. So lässt sich prüfen, ob der Harzfluss ausreichend ist, und die Kenntnis des Maximaldrucks ist hilfreich bei der Auswahl der Größe der Formmaschine.
Abb. 7 Beispiel für die zeitliche Variation des Drucks in jedem Teil eines geformten Produkts
■ Kettverformung
Die Verzugsanalyse verwendet die Ergebnisse der Abkühlungs- und Füllanalyse, um vorherzusagen, wie Schrumpfung und Verzug des geformten Produkts erfolgen werden. Sie simuliert auch den Grad der auftretenden Verformung. Die Form und die Angussposition, die den Verzug minimieren, können in der Produktdesignphase berücksichtigt und berücksichtigt werden.
Verzugsdeformationen treten auf, wenn Produkte nicht gleichmäßig schrumpfen. Es gibt drei Hauptursachen für Verzug: Unterschiede bei der Abkühlung, Unterschiede bei der Schrumpfung und Unterschiede bei der Ausrichtung. Moldlfow gibt Informationen zu den Hauptursachen aus, wenn die Option „Ursache für Verzug angeben“ aktiviert wird. Abbildung 8 zeigt das Ergebnis der Ausgabe von Informationen zu allen Faktoren.
Abb. 8 Beispiel einer Kettverformung
■ Druck bei V/P-Umschaltung
Mit V/P-Umschaltung ist der Wechsel vom Einspritzvorgang (Geschwindigkeitsregelung) zum Druckhaltevorgang (Druckregelung) gemeint, wenn geschmolzenes Harz durch die Schnecke in die Form eingespritzt wird.
Der Druck bei der V/P-Umschaltung gibt an, wie weit das Harz während des geschwindigkeitsgesteuerten Füllvorgangs eingefüllt wird. Während des Geschwindigkeitsregelungsprozesses sollte die Kavität nicht vollständig mit Harz gefüllt werden, und die nicht gefüllten Bereiche werden durch die Druckregelung vollständig nachgefüllt. Wenn der Haltedruck zu diesem Zeitpunkt zu niedrig ist, kann dies zu Einfallstellen führen, und wenn er zu hoch ist, kann dies zu Graten und Formbrüchen führen.
Die geeigneten Formbedingungen werden durch eine Füllanalyse ermittelt.
Abb. 9 Beispiel für Druck bei V/P-Umschaltung
■ Druck an der Einspritzstelle
Analysiert die zeitliche Druckschwankung in jedem Teil des Formprodukts während des Füll- und Druckhalteprozesses. Wenn in einem bestimmten Teil des Formprodukts oder in einigen Teilen des Formprodukts bei einem Formprozess mit mehreren Hohlräumen ein ungleichmäßiger Druck herrscht, liegt möglicherweise ein Strömungsungleichgewicht vor. Überprüfen Sie, ob Strömungsprobleme vorliegen und der Druck ordnungsgemäß gehalten wird.
Abb. 10 Beispiel für Druck an der Einspritzstelle
■ Formschließkraft
Die Formschließkraft ist die Kraft, die erforderlich ist, um die Form beim Befüllen mit Harz dicht zu halten. Der entsprechende Wert ergibt sich aus der Druckverteilung im gesamten Formprodukt. Basierend auf der zum Formen erforderlichen Formschließkraft muss eine Formmaschine mit der entsprechenden Größe ausgewählt werden.
Abb. 11 Beispiel für die Formschließkraft
■ Faserorientierungstensor
Bei Harzen, die Glasfasern enthalten, kann die Faserorientierung Probleme wie ungleichmäßiges Schrumpfen und schwache Festigkeit in einigen Richtungen verursachen. Bei faserverstärkten Harzen kann die Faserorientierungsanalyse verwendet werden, um die Faserorientierung und den Orientierungstensor (Orientierungsgrad) nach Abschluss des Formprozesses zu bestimmen. Um die Eigenschaften von faserverstärkten Harzen nutzen zu können, ist es wichtig, die Orientierungstrends im Voraus zu verstehen.
Abb. 12 Beispiel eines Faserorientierungstensors
■ Einfallstellenschätzung
Basierend auf Füllanalysen und Druckhalteanalysen können wir vorhersagen, wo und wie tief Einfallstellen in einem Formprodukt wahrscheinlich auftreten. Einfallstellen treten normalerweise auf der gegenüberliegenden Seite der dicken Wände, Rippen, Wülste und inneren Rundungen des Formprodukts auf. Durch die Analyse verschiedener Formbedingungen wie Form, Angussposition, Form- und Harztemperaturabnahme kann die Ursache für Einfallstellen identifiziert und Gegenmaßnahmen ergriffen werden.
Abb. 13 Beispiel einer Einfallstellenvorhersage
■ Schweißnahtschätzung
Durch die Füllanalyse lässt sich vorhersagen, wo Schweißnähte auftreten. Schweißnähte treten dort auf, wo Harz auf Harz trifft. Da Schweißnähte zu Festigkeitsverlusten und optischen Mängeln führen können, können sie weniger auffällig gemacht werden, indem die Angussposition an eine Stelle angepasst wird, die von außen weniger sichtbar ist, oder indem der Auftreffwinkel (der Winkel, in dem das Harz auf das Harz trifft) moderiert wird.
Abb. 14 Beispiel für die Vorhersage einer Bindenaht
Wie werden die Analyseergebnisse genutzt?
Wir erklären, wie die aus der Spritzgussanalyse gewonnenen Informationen auf das Produkt-/Formdesign und die Formprozesse angewendet werden können. Analysedaten können verwendet werden, um in Situationen, in denen Urteilsvermögen erforderlich ist, rationale und objektive Indikatoren zu erhalten.
■ Größe der erforderlichen Formmaschine
Um die geeignete Größe der Formmaschine zu bestimmen, ist es wichtig, die geeignete Größe der Formschließkraft, des Einspritzdrucks usw. zu kennen. Mithilfe einer Spritzgussanalyse können diese Werte ermittelt und die Größe der Formmaschine im Voraus berücksichtigt werden. Die Größe der Formmaschine steht in direktem Zusammenhang mit dem Formzeitplan und den Kosten und ist daher für die Produktionsplanung erforderlich.
■ Ermittlung der Liquidität
Anhand von Füllmuster, Druck, Harztemperatur und anderen Faktoren prüfen wir, ob das geformte Produkt ohne Überschuss oder Mangel mit Harz gefüllt werden kann. Wir tragen dazu bei, Probleme während der Formphase zu reduzieren, indem wir im Voraus untersuchen und Gegenmaßnahmen ergreifen, z. B. dünnwandige Bereiche oder schwer fließende Angusskanäle anpassen oder die Art des Harzes ändern.
■ optimale Angusslage
Anhand des Füllmusters, der Schweißnaht usw. überprüfen wir, welche Angussposition das Formen erleichtert und das Auftreten von Defekten verhindert. Es ist auch wichtig zu prüfen, ob eine Änderung der Angussposition nicht zu anderen Problemen führt, und durch Priorisierung und Beurteilung die optimale Position zu bestimmen.
■ optimale Formbedingungen
Optimale Formbedingungen ergeben sich aus V/P-Umschaltdruck, Einspritzposition, Formtemperatur und Abkühlrate. Das Einstellen der Formbedingungen erfordert Erfahrung und Wissen und wird daher oft dem Können des Formtechnikers überlassen.
■ optimale Kühlung der Form
Basierend auf der Temperaturverteilung der Form und der zeitlichen Temperaturschwankung werden die Position der Wasserrohre und die Kühlwassertemperatur angepasst, um die Form möglichst gleichmäßig zu kühlen. Eine ordnungsgemäße Kühlung ist wichtig, da eine unzureichende oder ungleichmäßige Kühlung zu Formfehlern führen kann. Wenn nach Produktionsbeginn Formprobleme auftreten, ist es schwierig, größere Änderungen an der Form vorzunehmen, z. B. das Auswechseln der Wasserrohre. Daher ist es wichtig, dies im Voraus gründlich zu überlegen und Gegenmaßnahmen zu ergreifen.
■ Verbesserung der Kettverformung durch obige Optimierung
Ungleichmäßiger Druck, ungleichmäßige Kühlung und Faserausrichtung können zu Verformungen in Formprodukten führen. Insbesondere bei Produkten, die eine strenge Maßgenauigkeit erfordern, kann eine Spritzgussanalyse verwendet werden, um so viel wie möglich im Voraus zu überprüfen und Gegenmaßnahmen zu ergreifen, um Verformungen zu minimieren.
Einige der häufigsten Formfehler
Mithilfe von Spritzgussanalysen lassen sich mögliche Formfehler und -ausfälle vorhersagen. Formfehler sind bei der Massenproduktion von Gussteilen ein unvermeidbares Problem, und Spritzgussanalysen können dazu beitragen, ihr Auftreten zu minimieren. Einige der häufigsten Formfehler sind unten aufgeführt.
■ Kurze Aufnahmen
Unter „Short Shots“ versteht man einen Formfehler, bei dem das geschmolzene Harz die Spitze der Form nicht vollständig füllt. Geformte Produkte mit „Short Shots“ können nicht wiederhergestellt werden. Short Shots werden durch unzureichenden Harzfluss, unzureichenden Einspritzdruck oder unzureichenden Haltedruck verursacht. Kontrollieren Sie das Auftreten, indem Sie die V/P-Umschaltdruckposition, den Einspritzdruck und die Angussposition anpassen.
Abb. 15 Beispiel für kurze Aufnahmen
■ Bindenähte
Beim Zusammenfluss von geschmolzenem Harz in einem Formprodukt kann sich eine dünne kratzerähnliche Linie bilden, die als Schweißnaht bezeichnet wird. Diese Schweißnaht ist schwach und kann bei Festigkeitstests beschädigt werden. Sie kann auch äußerlich wie Kratzer aussehen, was zu Beschwerden seitens der Verbraucher führen kann. Gegenmaßnahmen sind beispielsweise eine Änderung der Angussposition, sodass die Schweißnaht nicht in markanten Bereichen erscheint, eine Anpassung der Formtemperatur und eine Anpassung der Dicke des Formprodukts, um den Auftreffwinkel zwischen zwei Schmelzfronten zu steuern. .
Abb. 16 Beispiel für Bindenähte
■ Brandflecken
Brandflecken sind ein Phänomen, bei dem ein Teil eines geformten Produkts verbrennt und schwarz und verkohlt wird. Dies geschieht, wenn das geschmolzene Harz unter hohem Druck eingespritzt wird, wodurch die Luft in der Kavität ihren Platz verliert und komprimiert wird, wodurch große Hitze entsteht. Brandflecken treten in der Regel nicht in den frühen Phasen des Formens auf, sondern wenn die Massenproduktion anläuft, und der Formprozess wird oft durch die Notwendigkeit erschwert, Brandflecken zu vermeiden. Neben der Reduzierung der Einspritzgeschwindigkeit ist es effektiv, Entlüftungsöffnungen vorzusehen, um Gas abzulassen und den Harzfluss durch Ändern der Angussposition und der Wandstärke zu steuern.
Abb. 17 Beispiel für Brandflecken
■ Einfallstellen
Einfallstellen sind eine Art optischer Defekt und werden durch unterschiedliche Schrumpfungsraten an verschiedenen Teilen des geformten Produkts verursacht, beispielsweise durch unterschiedliche Wandstärken. Dies kann durch Anpassen der Angusspositionen, Erhöhen des Einspritzdrucks, der Kühlleistung und Anpassen der Wandstärke behoben werden. Da dieser Defekt tendenziell in dickeren Abschnitten wie Rippen und Vorsprüngen auftritt, ist es wichtig, bereits in der Entwurfsphase Gegenmaßnahmen zu ergreifen.
Abb. 18 Beispiel für Einfallstellen
Zusammenfassung
Es ist wichtig, während der Produkt- und Formdesignphase mögliche Probleme im Formprozess zu simulieren und Gegenmaßnahmen zu ergreifen. Zu diesem Zweck müssen Designer auch über Kenntnisse im Formprozess verfügen. Wenn beim Design die Formbarkeit berücksichtigt wird, verringert sich die Nacharbeit und die Entwicklungszeit wird unmittelbar verkürzt. Nicht alle Formprobleme können allein im Formprozess behoben werden. Es ist notwendig, bereits in der Designphase Gegenmaßnahmen zu ergreifen, den Umgang mit CAE-Simulationsergebnissen zu erlernen und diese in Ihrem Design optimal zu nutzen.
Nächster Teil: „Vorhersage von Formfehlern“
Für weitere Informationen zu CAE kontaktieren Sie uns bitte.
CAE-Download-Folien
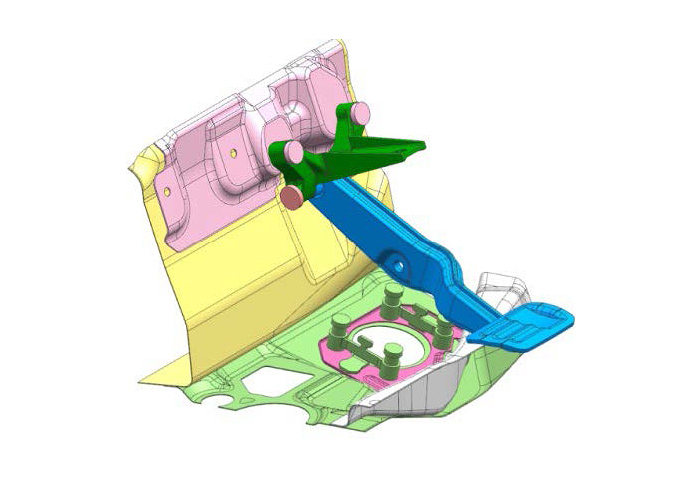
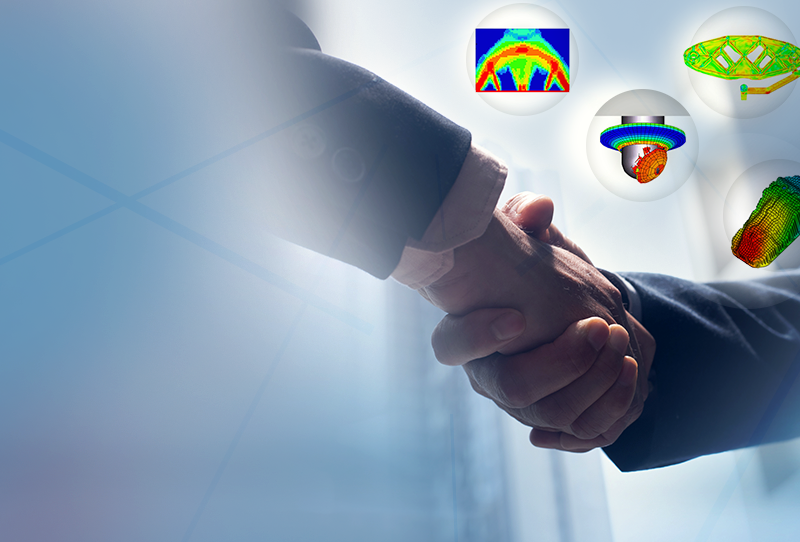