- TOP
- CAE解析の基礎知識
- 第7回 樹脂流動解析による成形不良の予測
<連載>プラスチック製品設計のためのCAE解析基礎知識
第7回 樹脂流動解析による成形不良の予測
流動解析は、設計段階で成形不良を予測し事前に対策を講じるための貴重なツールです。
今回は、各種成形不良と事前対策に活用できる解析評価項目について紹介します。
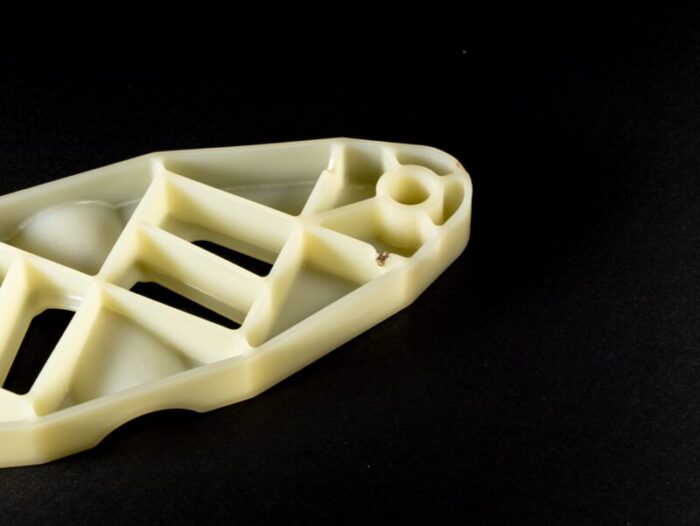
目次
1. はじめに |
2. 流動解析の評価項目と不良現象について |
3. 直接アウトプットできる不良現象 |
4. 他の評価項目から推察できる不良現象 |
5. 予測が困難な不良現象 |
6. まとめ |
はじめに
第6回の後半では、流動解析を行うことにより、ヒケや反り、ウェルドラインなどの成形不良も予測できることを紹介しました。第7回では、成形不良に視点を置いて、流動解析のどの評価項目がどの不良現象に活用できるのか、もう少し詳しく解説していきます。
流動解析の評価項目と不良現象について
成形不良は、設計段階で解析を行うことで、事前に確認し対策を練ることができるものとそうでないものがあります。また、ソフトウェアの評価項目になくても、解析結果から推察できるものもあり、それらを知っておくことで解析結果をより活用することができます。
下表に、成形不良現象とそれぞれに活用できる解析評価項目をまとめました。
「評価項目の有無」欄の記号は以下を示しています。
●:シミュレーションツールから直接アウトプットできる
〇:右側の評価項目から推察することで評価できる
▲:現在ソフトウェアメーカーで開発が検討されている
×:シミュレーションからの予測は困難
図1 成形不良現象と樹脂流動解析での評価項目の対応表
それぞれの成形不良現象について説明しましょう。
直接アウトプットできる不良現象
■ ヒケ
ヒケとは成形品の肉厚が異なる箇所、特に裏面にリブやボスなどが立っている表側に発生する成形不良です。成形品表面がくぼんでしまうため、意匠面など外観を重視する製品では注意が必要です。ヒケが大きい場合は寸法精度が問題となることもあります。
ヒケは冷却時の熱収縮の際に、収縮率に差が生じることで発生します。充填解析、保圧解析から、ヒケの発生箇所や深さをシミュレーションして評価できます。
図2 ヒケ例
■ 反り
薄肉部と肉厚部の収縮差や、冷却時の収縮差、繊維配合材料の配向、残留応力などによって成形品が反ってしまう現象のことです。成形後、時間をおいて発生することもあるため、注意が必要です。成形不良になるだけでなく、組立てが必要な部品では寸法不良や、はめ合わせ不良にもなります。
反り解析を用いることで、変形図や変位量をシミュレーションできます。
■ ウェルドライン
成形品内に充填された溶融樹脂の合流部分が線状になって現れる成形不良です。薄い傷状に見えるため、成形不良となるほか、ウェルドラインの発生箇所では強度が落ちるため、破損の原因となる恐れもあります。
充填解析を行うことで、ウェルドラインの発生箇所を予測できます。ウェルドラインを完全に消すことは困難ですが、ゲート位置などを調整して見えにくい場所に移動させたり、薄くさせたりする対策をとることができます。
図3 ウェルドライン例
■ ヤケ(焼け)
成形品の一部が焼けて黒く炭化してしまう成形不良です。ガス焼け、ガスとも言います。成形時に樹脂材料内の空気や揮発性ガスが金型内に閉じ込められ、圧縮されたことで高温となり、樹脂が焼け付くために発生します。
エアベント解析をすると焼け指標結果が生成されます。金型内のガス抜け情報を漏れなく入力する必要があるため、非常に難易度の高いシミュレーションになります。
図4 ヤケ例
■ エアートラップ
複数の溶融樹脂が合流する際に、空気やガスが閉じ込められた状態をエアートラップと言います。気泡(バブル)となり、成形品表面に小さい穴が生じるほか、強度不足の原因にもなります。重度の場合、ヤケが発生する恐れもあります。
フローパスのバランスが悪い、流動が不均一な箇所などに発生しやすく、充填時間結果を確認することで発生箇所を予測できます。
他の評価項目から推察できる不良現象
■ジェッティング
ジェッティングとは、金型内に射出された樹脂が折り重なるように蛇行して流動した跡が、成形品表面に模様として出てしまう成形不良です。ゲート周辺に発生しやすく、強度不足の原因にもなります。
充填解析の充填領域結果で、樹脂の蛇行状流れを確認することで、ジェッティングの発生を予測できます。
■フローマーク
フローマークとは、射出時に生じた樹脂の流れ模様のことです。さまざまなフローマークがありますが、ゲート周辺に同心円状の波紋のような模様が現れるといった成形不良となります。低い金型温度や樹脂温度、保圧不足などが発生の原因です。
充填解析のメルドラインから間接的に予測できます。メルドラインとは樹脂が合流する際にウェルドラインよりも会合角が大きい状態を示し、一本の線として示されます。この箇所にフローマークが発生する恐れがあるということです。
■タイガーストライプ(タイガーストライプ・フローマーク)
成形品の表面に低光沢部と高光沢部が交互に、しま模様のように繰り返し現れるフローマークです。単純なフローマークの場合に比べ、複雑な流動が起きたことで発生するため、流動パターンを検証する際には経験も必要です。
解析ツールが解析結果として示せるよう、ソフトウェアメーカーで開発が進められています。
■ショートショット(充填不足)
溶融した樹脂が金型の先端まで完全に充填されないという成形不良です。形状不良となる重大な成形不良です。
充填解析でフローパスが完全に充填されているか確認することによって、ショートショットの発生を予測できます。
図5 ショートショット例
■ ボイド
成形品内にボイド(気泡)が発生するという成形不良です。透明成形品であれば成形不良になります。また、応力集中によって割れやすくなる、強度が不足する原因にもなります。樹脂の冷却時に、冷えやすい表面へ樹脂が引き寄せられてしまうことで発生します。気泡は、発生直後には真空泡ですが、時間がたつと空気が入り込みます。肉厚部の内部にできやすい傾向があります。
充填解析の体積収縮率と充填パターンや充填時間から間接的にシミュレーションできます。発生原因はヒケと近似しているため、基本的な対策はヒケ対策と同じです。
■ ためらい(へジテーション)
ためらい(ヘジテーション)とは、樹脂が注入される際に、溶融樹脂が流れやすい厚肉部などが先に充填されることで、薄肉部などに樹脂が流れていかなくなってしまう状態のことです。ためらいはショートショットやヒケなどの成形不良、外観品質のばらつきなどの原因となります。
充填時間結果を確認することで、ためらいが発生している恐れがあるかどうかを確認できます。
■ アンダーフロー
溶融樹脂が二方向から合流した際に、一方の樹脂が逆流することをアンダーフローと言います。すでに固化した樹脂が再溶融することで、成形品の外観や強度に問題が発生する恐れがあります。
充填パターンのアニメーションによって、フローフロント合流部の流動方向が反転していないかどうかを確認できます。現在は充填パターンのアニメーションを通して確認することで予測しますが、解析結果として確認できるよう、ソフトウェアメーカーで開発が進められています。
■ 割れ
成形品が破断したり、亀裂が発生したりする現象のことです。成形後、時間がたってから発生する場合があります。
ウェルドライン部の強度不足によって割れが起こる場合は、ウェルドラインの肉厚方向(ウェルドサーフェス)を3Dで確認することで予測できます。成形品の残留応力によって発生する場合は、肉厚方向に発生している最大せん断応力を確認することで割れの発生を予測できます。
予測が困難な不良現象
■ バリ
金型の合わせ面のすき間などから樹脂が押し出され、薄膜状に成形されてしまう成形不良です。手作業で除去するなどの追加工程が発生します。
型締力の不足、強すぎる圧力などの原因で発生しますが、金型の物理的な問題などから発生することも多く、シミュレーションによる予測は困難です。
■ シルバーストリーク
成形品の表面にすじ状の線や模様が現れる成形不良です。銀条、シルバーとも言います。
樹脂材料に含まれる空気や揮発ガス、水分などによって発生します。樹脂由来のため、シミュレーションでの予測は困難です。
■ カラーストリーク
成形品の表面に、樹脂の色ムラがすじ状に模様となって現れる成形不良です。
樹脂材料の着色材に起因することが多いため、シミュレーションでの予測は困難です。
■ 剥離
成形品内に膜状の層ができ、ポロポロと剥がれてしまう成形不良です。成形不良、形状不良となります。
相性の悪い樹脂の混入などが原因で発生します。シミュレーションでの予測は困難です。
■ 変色
成形品が元の樹脂色から変化してしまう成形不良です。
着色剤の分散不良、樹脂の熱劣化による黄変など、成形材料が原因となることも多いため、シミュレーションによる予測は困難です。
まとめ
成形不良は成形の現場だけで全てを解決することは難しく、設計の段階でできるだけ対策を施しておくことが求められます。そのためには設計者も樹脂の特性や成形不良を知り、発生原因や発生原理を理解しておく必要があります。
また、成形不良は設計段階で解析を行うことで、事前に確認し対策を練ることができるものとそうでないものがあります。ソフトウェアの評価項目になくても解析結果から推察できるものもあるため、それらを知っておくことで解析結果をより活用することができるのです。
流動解析を用いた成形不良対策でご質問・ご不明点などございましたら、お気軽に“ お問い合わせ ”ください
次回は「ガスインジェクション成形への応用」についてご説明します。
CAEに関するお問いわせはこちらから