Summary
- 製品を製造する際に省資源化を実現する方法として「1. 材料使用量の削減」「2. 工程削減」「3. 端材再利用」の3つの方向性を取り上げます。
- 形状最適化・複数部品一体化・製品小型化により、材料使用量の削減が可能です。樹脂CAE技術を用いた最適形状提案事例をご紹介します。
- 組付け、塗装といった製造工程を最小限にすることで、労務費(人的コスト)や加工エネルギー、材料ロスを削減できます。アセンブリしやすい形状を実現する素材、塗装工程を削減できる製品をご紹介します。
- 製造工程で出た樹脂端材を破砕し、一定割合を製品に混ぜ再利用するリグラインドにより、トータルとしての樹脂使用量を削減できます。熱安定性・リグラインド性に優れる素材をご紹介します。
モノづくりと省資源化
環境に配慮しながら製品を製造する方法の一つに「省資源化」、以前より知られている3Rの「リデュース」があります。本ページでは、下記3つの方向性から省資源化の方法をご紹介します。
省資源化への 3つの方向性
- 材料使用量の削減 :形状最適化・小型化による製品重量の削減、部品点数削減による材料使用量の削減
- 工程削減:部品点数削減 あるいはアセンブリしやすい形状による組付け工程レス、外観に優れた素材の採用による塗装工程レス
- 端材の再利用 :これまで廃棄されてきた端材をリグラインド材として再利用することにより、材料使用量の削減
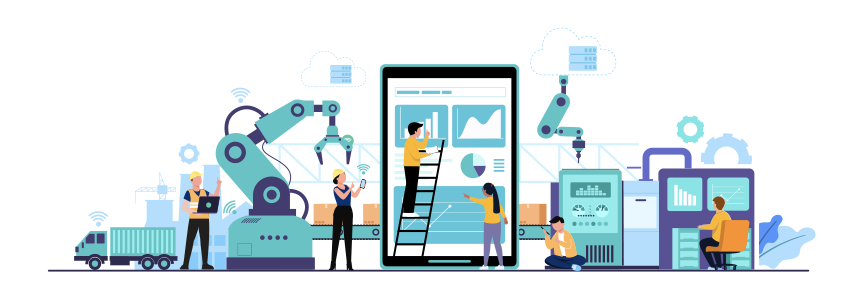
材料使用量削減と工程削減
私たちが日常生活で用いている電化製品や自動車などは、複数の部品から構成されます。その製造過程には、部品の成型から組み立て、塗装に至るまで複雑な工程が組まれています。
これらの工程を最小限に減らすことで、労務費(人的コスト)や後加工エネルギー、材料ロスを削減できます。また、樹脂の材料使用量の削減や塗装剤レスにすることで、製品製造時の省資源化に貢献できます。
① 材料使用量の削減
A. 部品点数削減と最適形状・軽量化による樹脂使用量の削減
製品の形状を工夫することで、従来複数から成り立っていた部品の一体化による部品点数の削減や、小型化・軽量化が期待できる場合があります。樹脂CAE技術の活用は製品を設計する際に最適な形状を考案する有効な方法のひとつです。
B.塗装レス素材の採用
表面外観・耐候性に優れている素材や、塗装をせずにメタリック調などの表現が可能な素材を採用することで、塗装工程の削減やメッキ・溶剤の使用削減に繋がります。(これは以下ご説明する②工程の削減にもあてはまる解決策になります)
②工程の削減
A. アセンブリしやすい形状の採用
エンジニアリングプラスチックは金属に比べ形状自由度が高いため、アセンブリしやすい設計を実現できます。アセンブリしやすい設計により組み立て工程が省略されると同時に、従来使用していたねじやボルトが不要となり省資源化に貢献します。
B. 後工程が不要な、成形性が良い材料の採用
製品を製造する際、発生したバリを取るバリ取りや、反りや歪みを改善するアニール等の二次加工が必要な場合があります。バリや反りが発生しにくい素材等を用いることにより、後工程が省略できる可能性があります。
端材の再利用
樹脂を利用した製造工程で発生するスプルー・ランナーといった端材を製造者の元で破砕し、成形材料として再生した樹脂をリグラインド材と呼びます。一般的に、リグラインド材は各種性能が低下しない範囲で、新品の材料であるバージン材に一定割合で添加することが可能です。
従来は廃棄されていた端材を再利用することにより、樹脂使用量の削減に貢献することが可能です。
旭化成からのご提案 ①
工程・部品の削減
アセンブリしやすい形状を可能にする変性PPE発泡ビーズ サンフォース®
サンフォース®は、軽量、断熱性という発泡体ならではの性能に加えて、難燃性(UL-94 V-0)、寸法精度、薄肉成形などの、従来の発泡体を超えた機能を併せ持った発泡体です。加工時の寸法変化も非常に小さく、一般的な射出成型品に近いレベルでの成形加工が可能です。寸法精度を求められる構造体やシャーシにも安心して使用いただけます。
また、サンフォース®は樹脂の中でも線膨張係数の少ないPPE樹脂の特徴を引き継ぎ、温度による影響は比較的小さくなっています。
さらにサンフォース®は、金型内にビーズを充填してスチームでビーズ同士を膨らませながら熱融着させる方法です。そのため、高温高圧で樹脂を金型に流し入れる射出成型とは異なり、成形品肉厚に厚い部分と薄い部分の偏肉がある場合でも反りやヒケが出にくい特徴があります。そのため、均一な肉厚にするなどの形状制限もなく自由に設計いただくことが可能です。
このような賦形性を活かし、例えば基板やハーネスに沿った形状で成形品を作り上げることで、部品パック内のアセンブリ時に部品固定用のねじ・ボルトを減らすことも用途によっては可能となり、省行程でご使用いただくことができます。
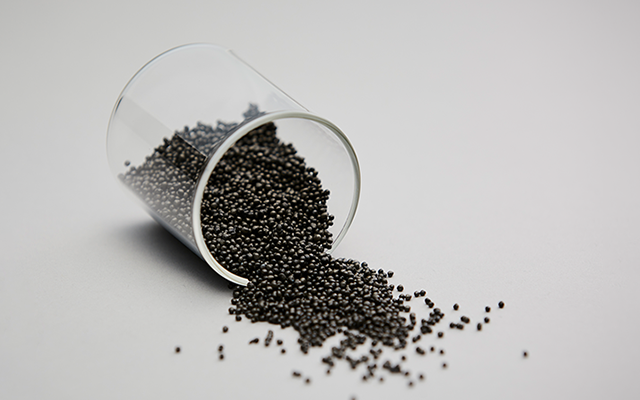
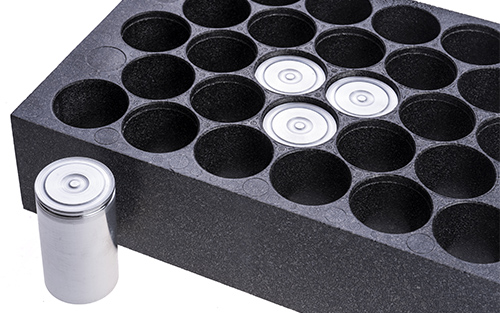
塗装レスによるコストダウン・環境負荷低減が可能なメタリック調ポリアセタール (POM) 樹脂
ポリアセタール(POM)樹脂は、機械物性、摺動性、耐薬品性に優れるため、多くの機構部品や内装部品に使用されています。
旭化成のPOM樹脂「テナック™-C ZM413」は、一般耐候グレードと同等の物性及び耐候性を有し、自動車OEM各社の車室内環境基準(揮発成分の低減)にも対応するメタリック調POMコポリマーです。
一般的にメタリック調の部品を得るにはベース樹脂の表面に塗装やメッキをする手法が用いられますが、これらの複数の工程でコストがかかることや、一部の工程において溶剤を用いることから環境汚染の懸念があることが欠点です。テナック™-C ZM413を使用することで塗装工程を省略し、これらの欠点をカバーすることが可能です。

- メタリック調POM樹脂 テナック™-C ZM413の詳しい説明はこちら
樹脂CAEを活用した金属部品からの樹脂化による軽量化
旭化成には、樹脂に特化した解析技術である「樹脂CAE技術」がございます。
樹脂CAE技術をどのように活用しているのか、下図の解析事例をご紹介します。この事例では、
The original product (far left image) was made of steel and consists of multiple components.
トポロジー最適化解析を活用することで、the product was made from resin instead of steel 複数の部品で構成される鉄製の自動車ブレーキブラケットを80%以上軽量化できる、樹脂製ブレーキブラケットの設計案を創造しました。
旭化成の「樹脂CAE技術」をご活用いただくことで、製品の利用シーンで想定される構造的な制約、様々な荷重・拘束条件の下で、設定した設計空間において、最も効率の良い材料の分布を見つけ出すことができます。
また、解析で得られる形状は非常に自由度が高く、下記の事例では解析技術者の経験と融合させることで、今ある設計や既存概念にとらわれない新しい形状の射出成形品を考案することができました。検討を重ね不要な箇所を特定し、更に形状を簡略化することで、最終的に「部品点数削減」と「超軽量化」を実現しています。
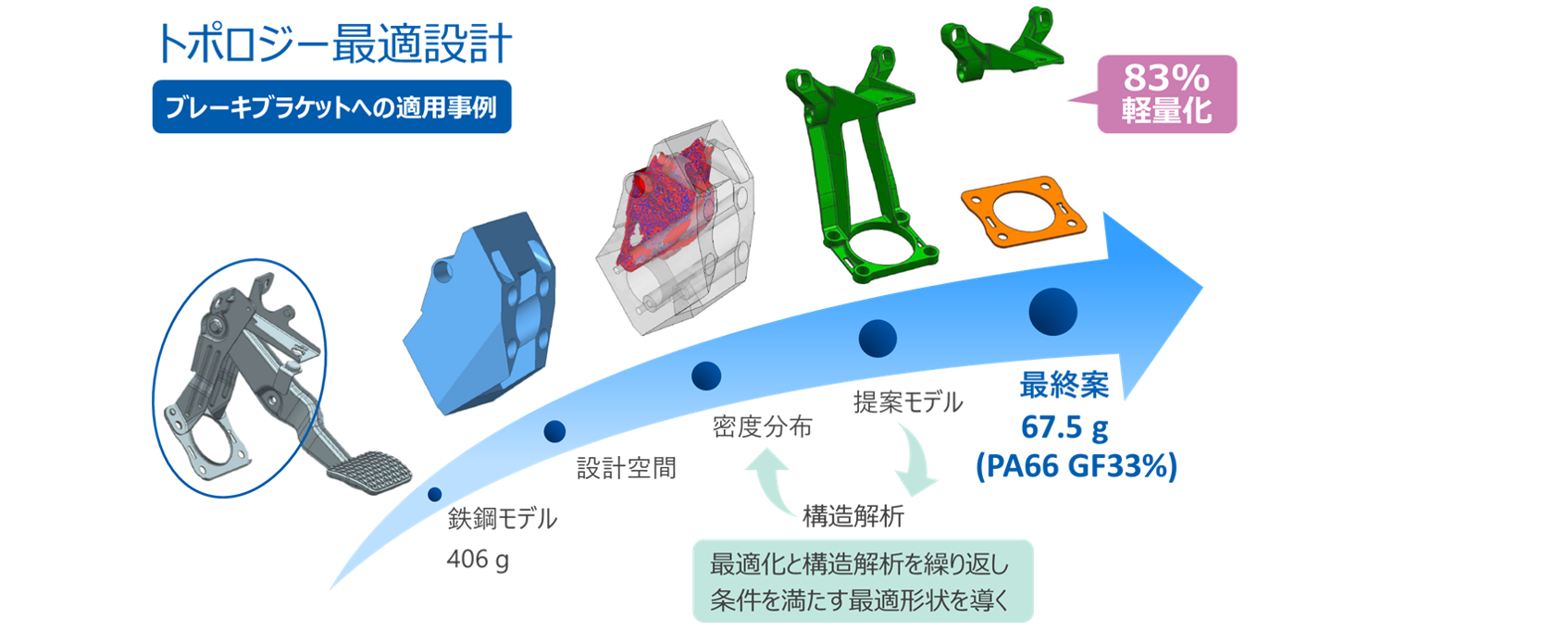
メッキレス・無塗装 高強度・高外観ポリアミドによる蝶番の金属代替事例
主にドアや戸に用いられる蝶番には高い強度が求められることから金属ダイキャストが一般的に使用されていますが、意匠性の観点からメッキによる加飾が必須であり、金属イオンを含む廃液が発生・処理が発生し、環境への負荷が大きいという課題があります。
ポリアミド樹脂「レオナ™」SGシリーズは、蝶番としての機能を満たすことはもちろん、メッキレスかつ無塗装での製品化を実現し、軽量化に加え、製造工程における廃棄物削減で環境に貢献できます。
後加工レス・軽量化による輸送エネルギー削減 高強度ポリアミドによる空圧機器筐体の金属代替事例
製造現場を支える空圧制御機器筐体は、高い強度が求められるため主に金属で作られています。一方で、空気をコントロールするために微細な流路加工が施されており、加工エネルギーと材料ロスが発生します。これを、高強度を特徴とする「レオナ™ Sシリーズ」に置き換えることで、後加工を省略でき、工数削減に寄与します。
また、空圧制御機器は全世界に供給されるため、金属よりも軽量な樹脂製にすることによる製品重量低減効果により、輸送エネルギー削減にも貢献できます。
旭化成からのご提案 ②
端材再利用
リグラインド性に優れた変性PPE樹脂「ザイロン™」
変性PPE樹脂 「ザイロン™」は、熱安定性と耐加水分解性に優れた樹脂で、リグラインド時に物性劣化を起こしにくいことから、他樹脂に比べ再生利用しやすい材料です。また、エンジニアリングプラスチックの中で最も比重が軽く、軽量な素材であることから、製品を作る際に素材使用量が少なくてすみます。
これらの性質を活かし、変性PPE樹脂を用いて製品を製造することと、製造工場内で発生するスプルー・ランナーなどを再生利用することにより、トータルとしての素材使用量を減らすことができ、環境負荷低減に寄与できると考えます。
*一部、外観重視の用途などでは、再生品利用に起因した異物混入などの外観不良を招くおそれがありますので、再生品の利用には慎重を要します。再生品を利用する場合は、再生比率20%までを目安にしてご検討下さい。
ご提案に関する各種ご質問・サンプルのご依頼をお待ちしております。ご興味をお持ちいただけましたら、是非お気軽にご連絡ください。
お問い合わせ