Technische Informationen
Details zur Spritzgussanalyse
Bei der Spritzgussanalyse sind Füll- und Packanalyse sowie Verzugsanalyse wichtige Simulationen im Spritzgussprozess.
Abfüll- und Packanalyse
Bei der Füll- und Packanalyse handelt es sich um eine Analyse, die simuliert, wie das Harz in die Form fließt (Füllvorgang) und wie die nachfolgende Packphase abläuft (Anwenden von Haltedruck, um das Schrumpfen des Harzes zu unterdrücken). Im Einzelnen konzentriert sie sich auf die folgenden Punkte:
- Füllanalyse: Dabei wird simuliert, wie das Harz eingespritzt wird und den Hohlraum in der Form füllt (der Raum, der die Form des geformten Produkts bestimmt). Es wird bestimmt, ob ein Formen möglich ist oder nicht und welche optimalen Formbedingungen auf der Grundlage von Harzfluss, Fließgeschwindigkeit, Temperaturverteilung, Druckverteilung usw. gelten.
- Nachfüllanalyse: Nach Abschluss des Füllvorgangs wird der Vorgang des Anwendens von Nachfülldruck zum Ausgleich der Abkühlung und Schrumpfung des Harzes simuliert. Achten Sie auf Einfallstellen, Hohlräume und kurze Spritzer.
- Kühlanalyse: Simuliert das Kühlverhalten innerhalb der Form aufgrund von Wärmeleitung und Wärmeübertragung. Berechnet die Oberflächentemperatur der Form und die Temperaturverteilung des Harzes und berücksichtigt das Layout des Kühlkreislaufs und die Temperatur des Kühlmittels. Kann mit einer Füll- und Packanalyse gekoppelt werden.
.png)
Verzugsanalyse
Zusätzlich zur oben erwähnten Füll- und Packanalyse analysiert die Verzugsanalyse den Verzug, der während des Abkühlvorgangs des geformten Produkts auftritt. Sie simuliert den Verzug und die Verformung, die aufgrund ungleichmäßiger Schrumpfung auftreten, wenn das Harz nach dem Spritzgießen abkühlt und verfestigt.
- Verformungsanalyse: Prognostiziert Schrumpfung und Verformung von Formprodukten nach dem Lösen aus der Form basierend auf den Ergebnissen der Füll-, Verdichtungs- und Abkühlungsanalyse. Die Ursachen für Verformungen können in drei Faktoren eingeteilt werden: Abkühlungsunterschied, Schrumpfungsunterschied und Orientierungsunterschied. Sobald die Ursache identifiziert ist, können Lösungen wie das Ändern der Angussposition oder der Formbedingungen in Betracht gezogen werden.
.png)
Bewertung der Faserorientierung
Bei faserverstärkten Harzen mit Glasfasern muss die Faserausrichtung berücksichtigt werden, da diese erhebliche Auswirkungen auf die Produktleistung haben kann.
Um Informationen zur Faserausrichtung zu erhalten, wird der Faserausrichtungstensor aus der Spritzgussanalyse ausgegeben.
Hier zeigen wir, wie eine Auswertung anhand eines flachen Prüfkörpers durchgeführt wird (Abbildung 4).
Der Faserorientierungstensor ist eine Wahrscheinlichkeitsverteilung (0 bis 1) der Faserorientierung. Hier wird der Faserorientierungstensor in drei Richtungen ausgewertet: x-Achse, y-Achse und z-Achse. Wenn der Tensorwert zunimmt (nahe 1), bedeutet dies, dass die Fasern in jeder Richtung stärker ausgerichtet sind.
Der gemessene Wert des Faserorientierungstensors wurde mithilfe einer einzigartigen Methode aus dem Bild des Produktquerschnitts an der mit einem optischen Mikroskop beobachteten Bewertungsposition berechnet. Der Faserorientierungstensor wurde in 5 %-Intervallen in Dickenrichtung des geformten Produkts berechnet. Die stabförmigen und kreisförmigen Objekte im vergrößerten Bild von Abbildung 4 bestehen aus Glasfaser.
Abbildung 5 zeigt die Messungen des Faserorientierungstensors und die aus der Spritzgussanalyse erhaltenen Analyseergebnisse.
Man kann sagen, dass die Analyse in der Lage war, den tatsächlichen Faserorientierungstensor vorherzusagen.
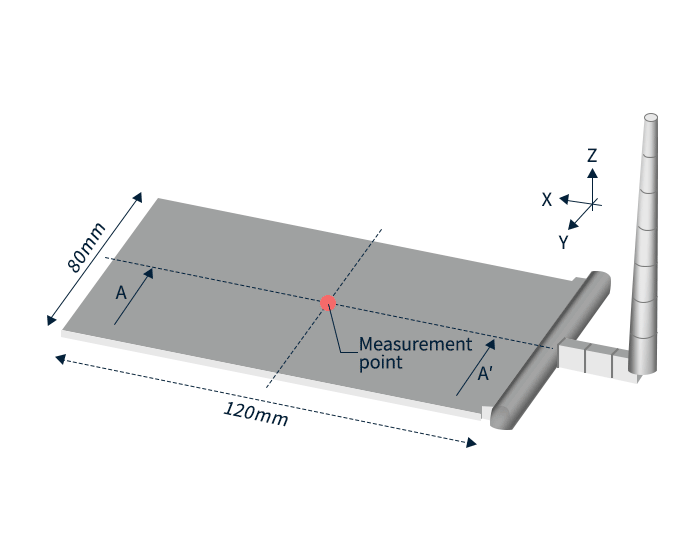
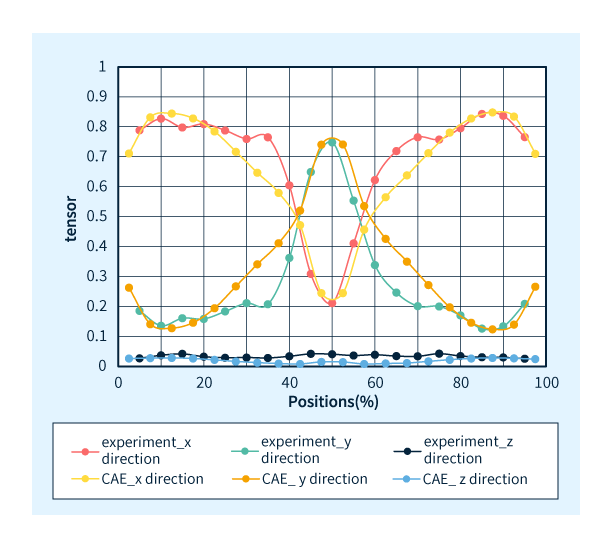