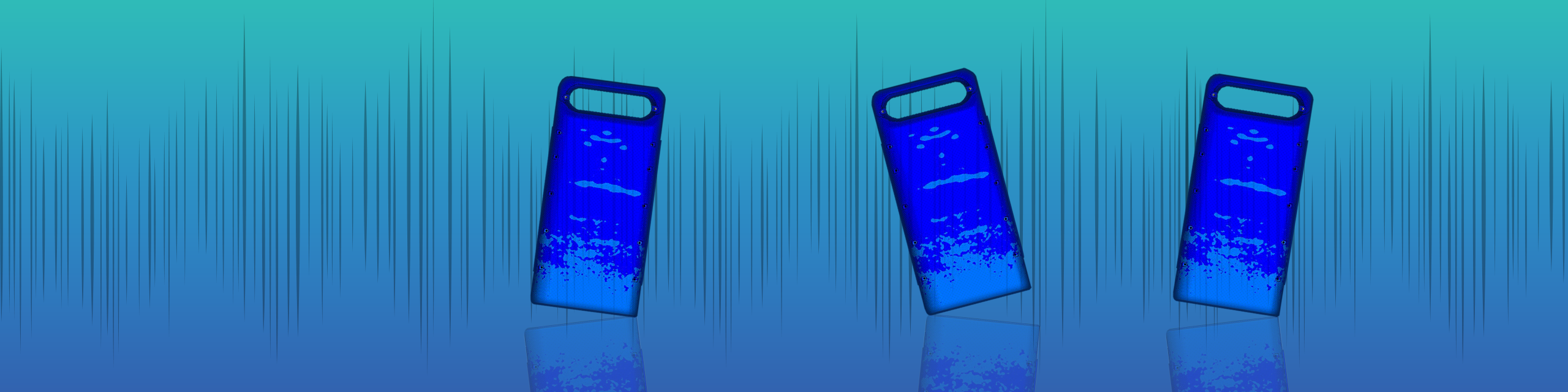
動的構造解析事例
UN R136に基づく落下試験シミュレーション: バッテリーケース
目次
Summary
- バッテリーケース、セルホルダーに採用されたザイロン™の落下解析の事例を紹介します。
- UN R136に基づく1m落下解析で検証した成形品が実際の落下試験で合格しました。
解析の背景
ケースを樹脂化した際に破壊の懸念があったため、形状変更しながら落下解析と流動解析を実施して性能や成形性に問題がないことを確認した後、試験に至りました。
リチウムイオン電池の耐久性を評価するために実施される一つの安全性検証方法が落下試験です。この試験では、電池を特定の高さから決められた方法で(角度や部分を指定して)、予め指定された素材の床に落とすことにより、その耐衝撃性能を測定します。
Here, we present a case study of a drop test simulation that adopted the standards of UN R136, specifically for XYRON, which is used in actual battery cases and cell holders.
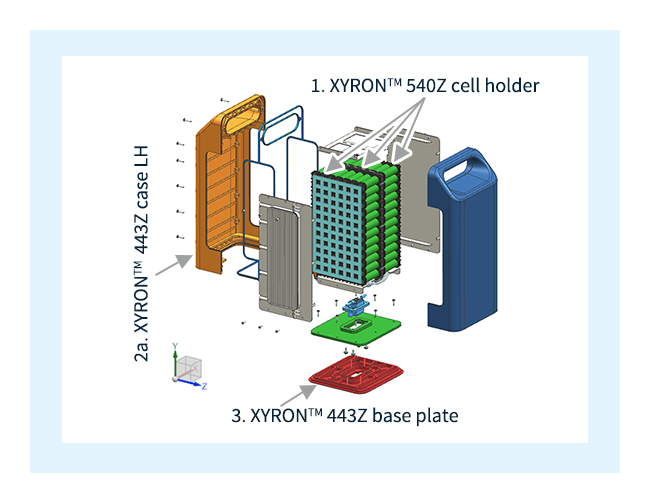
バッテリーケース、セルホルダーに採用されたザイロン™
目的
バッテリーケースの落下衝撃に対する耐久性、衝撃を与えた状態の変化を確認する
確認内容
落下解析により、バッテリーケースの耐久性を確認しました。
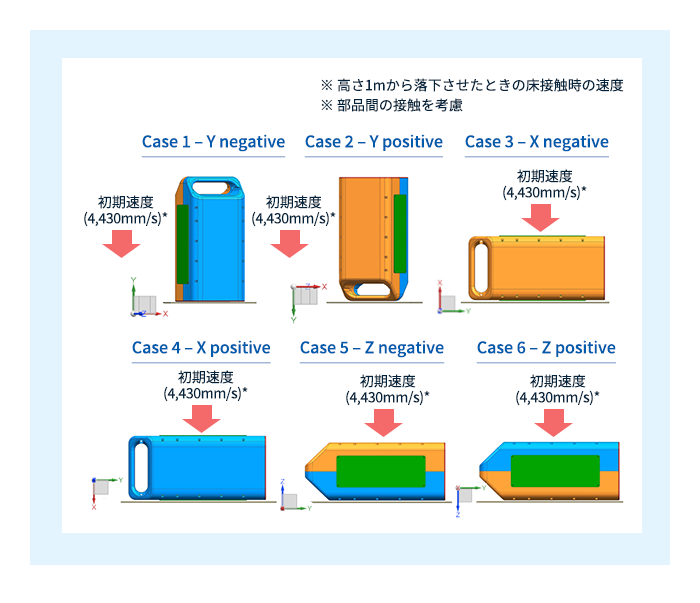
落下試験シミュレーションの条件
解析結果
落下試験はAIS-156 Annex8C「Mechanical drop test for removable REESS 」に準拠しました。
また、体(エンクロージャ)による保護等級はIPXXBが指定されており、クラックが発生する場合、クラック径は12mm未満になる必要があります。
下記にて、実際のシミュレーション結果をお見せします。
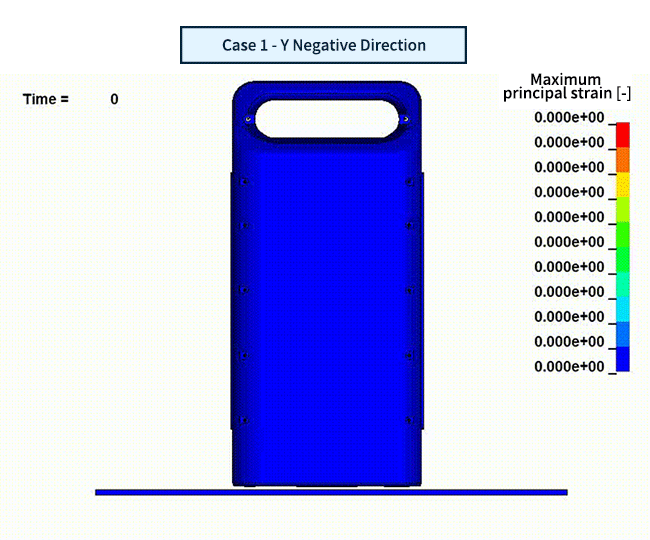
Case1の場合のシミュレーション結果
落下解析では、クラックはX方向とY方向の落下でのみ発生すると予測されましたが、クラックサイズはいずれの方向の落下でも10mm以下であり、問題ないことが解析から確認でき、ザイロン™製バッテリーケースの認証に成功しました。
落下試験シミュレーション結果
Analysis case | Material | Direction | Crack size(mm) *** |
Criteria | Evaluation |
---|---|---|---|---|---|
Case 1 | Xyron 443Z |
Y-Negative | 3.23 | Crack size less than 10 min | OK |
Case 2 | Y-Positive | 1.31 | |||
Case 3 | X-Negative | 0.99 | |||
Case 4 | X-Positive | 0.88 | |||
Case 5 | Z-Negative | 0.00 | |||
Case 6 | Z-Positive | 0.00 |
<その他の検討事項>
CAE解析に関するご質問・ご相談などはこちらへ
お問い合わせ