- TOP
- Basic knowledge engineering plastics
- What are engineering plastics?
What are engineering plastics?
An overview of the various types of engineering plastics and their characteristic physical properties
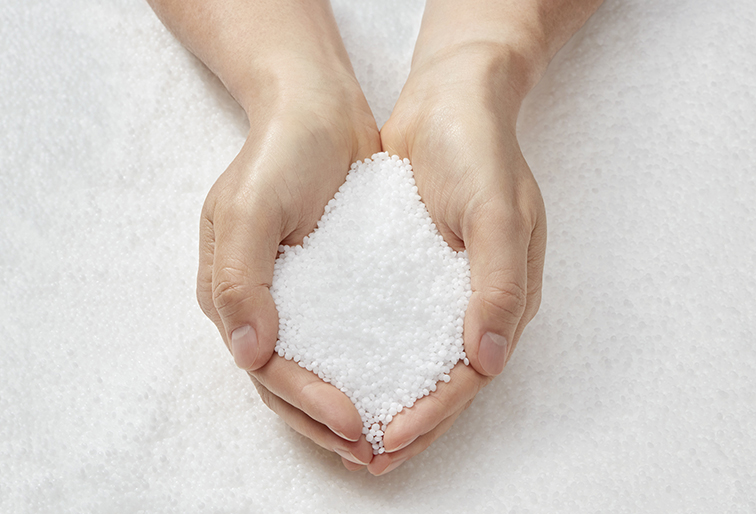
1. Plastics: A brief introduction
Engineering plastics is the collective term for a family of plastic materials offering excellent strength and heat resistance. More specifically, engineering plastics are highly functional resins with typical heat resistance above 100°C, strength above 49 MPa (500 kgf/㎠), and bending modulus above 2.4 GPa (24,500 kgf/㎠).
Appreciating the unique properties of engineering plastics requires a basic understanding of plastics in general. Plastics are substances whose chemical structures consist of chain polymers; as shown in Figure 1, these are elongated molecules, in which as many as 1,000 or more carbon atoms are chained together in a flexible structure that can move relatively freely in isolation. However, when these long molecules are packed together they become so closely intertwined that it is difficult—at least at ordinary temperatures—for any one molecule to separate from the others. At high temperatures, on the other hand, molecular motion is activated and the forces constraining neighboring molecules gradually relax, allowing molecules to move with greater freedom. This is why plastics melt at high temperatures.
Figure 1: Schematic depiction of chain polymers comprising chemical structure of plastics.
Source: Based on Isao Sato (2001), Plastics: An Illustrated Guide (Natsumesha Co., Ltd.) (in Japanese)
When plastics rupture or deteriorate in solvents, it is because their elongated molecules become separated from each other. However, the length of the molecular chains comprising typical plastics is sufficient to ensure that molecules tend not to separate under ordinary usage conditions.
These behavioral properties of chain polymers suffice to explain the most important features of plastics:
(1) Their strength and hardness are sufficient to withstand practical applications.
(2) They are solids at room temperature.
(3) At higher temperatures they melt and can be molded into nearly any shape.
2. What are engineering plastics?
Among the various types of plastics, the term engineering plastics refers to a particular family of plastic materials offering unusually high performance. To prevent melting—even at high temperatures—and minimize degradation in the presence of solvents, the molecular chains in plastics must be prevented from moving. As described in Column 1, there exist various strategies for achieving this; for engineering plastics, the most common approach is to insert atoms other than carbon (denoted X in Figure 2) into molecular chains.
C-X bonds suppress molecular motion more than C-C bonds, increasing melting temperatures; inserting benzene rings instead of single atoms yields even greater motion-suppressing effects.
Figure 2: Techniques for improving performance of chain-shaped polymers
3. Types of engineering plastics
Among the various categories of engineering plastics, the most widely used are known as general-purpose engineering plastics, of which the five most important varieties are known as the five major engineering plastics.
Achieving further performance enhancements typically requires exploiting the advantages of benzene rings. Engineering plastics made with a higher concentration of benzene rings in primary chains—thus improving various physical properties, especially heat resistance—are sometimes known as super engineering plastics.
4. Overview of the top five engineering plastics
Table 1 presents an overview of the five major engineering plastics.
Table 1 The 5 major engineering plastics: Comparison of key features
The upper three varieties are crystalline resins (see Column 2), listed in order from highest to lowest crystallinity. The lower two varieties are non-crystalline resins. Among all general-purpose engineering plastics, polycarbonate is the only transparent non-crystalline resin. Although modified polyphenylene ether (PPE) is also non-crystalline resin, PPE is rarely used in isolation; instead, it is typically used as a polymer alloy material (Column 3). Pure PPE features high heat resistance, but is difficult to form into complex shapes; alloying with other resins such as polystyrene yields materials that are readily formable while offering a range of desirable properties.
In what follows, we briefly survey key features of the five major engineering plastics.
Polyacetal (POM)
Of the five major engineering plastics, polyacetal has the highest crystallinity, ensuring excellent abrasion resistance that makes it an ideal material for gears, axle mounts, and other components required to withstand frequent sliding motion. POM exists in two varieties: homopolymer and copolymer (Column 3). Homopolymer POM has a high melting point and excellent strength and rigidity, while copolymer POM is flexible and offers excellent resistance to heat-induced degradation, chemical resistance, and weather resistance.
Polyamide (PA)
Polyamide (PA) exists in many varieties, of which the two general-purpose engineering plastics most commonly used as structural materials are PA6 and PA66. PA is a crystalline resin in which strong intermolecular forces, derived from the presence of amide groups, ensure excellent mechanical properties and resistance to solvents. Among the most widely used grades of polyamide resins are specialized grades offering particularly high performance in specific areas such as flame retardance or heat resistance, as well as strength-reinforced grades made with glass fibers or other fillers.
In addition to the general-purpose engineering plastics PA6 and PA66, there exist many specialized varieties of polyamide resins, including PA612 and PA12, which incorporate fewer amide groups to reduce water absorption; PA610 and PA11, which are made from plant-derived ingredients; and PA4T, PA6T, and PA9T, which incorporate benzene rings to increase heat resistance.
Polybutylene terephthalate (PBT)
PBT, a crystalline resin whose primary chains contain benzene rings, offers excellent mechanical properties and resistance to solvents. This material also features low water absorption, good dimensional stability, and outstanding electrical properties, and is easily modified to add flame retardance or fiber reinforcement. These characteristics make PBT a widely-used choice of material for automotive and electrical components.
Polycarbonate (PC)
Polycarbonate (PC), a non-crystalline resin whose primary chains contain benzene rings, is the only transparent material among the general-purpose engineering plastics. PC is used to make lenses and other optical components, as well as optical storage media such as DVDs. Alloy materials formed by blending PC with ABS feature excellent impact resistance and good formation properties and are used for products such as home-appliance housings.
Modified polyphenylene ether(m-PPE)
M-PPE is a non-crystalline resin boasting the lowest specific gravity of all general-purpose engineering plastics, making it a good choice for lightweight components to facilitate product weight reduction. M-PPE features good heat resistance, good resistance to inorganic chemicals, and high dimensional precision; it is also relatively easy to make flame-retardant due to the combustion-resistance of PPE. Although, as noted above, PPE features high heat resistance, its poor moldability properties make pure PPE a difficult material to form into complex shapes. For this reason, PPE is often modified by alloying with polystyrene or other resins to yield easily-formable materials boasting a range of other desirable properties. In recent years, PPE has been blended with an increasingly broad variety of non-polystyrene resins to yield novel materials addressing a diverse spectrum of needs. The term M-PPE, short for "modified PPE," is intended to describe materials made especially easy to use by exploiting polymer alloys.
5. The environmental impact of engineering plastics
As compared to general-purpose plastics, the use of engineering plastics reduces the total volume of material ingredients needed to produce products of identical quality; moreover, the replacement of carbon atoms with other elements in primary chains helps reduce the volume of greenhouse gases emitted when products are burned after use.
Additionally, many of the ingredients used to produce engineering plastics—including alcohols, carboxylic acids, phenols, amines, and amides—are either plant-derived or are easily synthesized from plant-derived substances, facilitating efforts to reduce use of fossil-fuel resources. For example, castor oil—a key ingredient used to make polyamide 11 and polyamide 610—is plant-derived, while formalin, used to make polyacetal, is obtained from oxidation of methanol, which in turn may be produced by fermentation of plant-based ingredients.
Of the many products made from engineering plastics, industrial components are among the most important and numerous, while single-use plastics—the primary application for most general-purpose plastic materials—are rare.
The increasingly dire problem of global warming demands urgent attention to the goal of reducing environmental footprints in all walks of life—and engineering plastics are no exception: efforts to reduce material volumes and increase product lifetimes, in both the manufacture and usage of engineering plastics, are of central importance. Indeed, if the useful lifetime of a product is doubled, one can argue that its total environmental impact—from usage through discarding—is halved.
Thus the challenge of increasing the functionality—and extending the lifetimes—of a wide range of materials represents a key step toward minimizing harm to Earth's environment.
Column 1: Performance-enhancement strategies for chain-shaped polymers
The challenge of improving the material properties of plastics—including strength, chemical resistance, and heat resistance—can, with only slight oversimplification, be reduced to one overarching goal: restricting the motion of molecules. For example, the phenomenon of shape deformation occurs when neighboring molecules shift their dynamical configuration, while phenomena such as rupturing, melting, and dissolving are due to neighboring molecules separating from each other. Suppressing the occurrence of all such phenomena thus requires suppressing molecular motion, and there exist a variety of strategies for achieving this, of which the most important are summarized in Table 2.
Table 2: Techniques for enhancing performance and diversifying behavior in plastics
As shown in Table 2, performance may be increased in two main ways: by restricting the individual motion of molecules themselves, or by suppressing the intermolecular motion of molecules relative to other neighboring molecules. In the former case, the key factor is the length of the chain-shaped molecules in a plastic; the longer each molecular chain, the more its motion is restricted by the presence of neighboring chains, thus increasing performance. Performance may be further enhanced by inserting non-carbon atoms or benzene rings in molecular chains to increase their rigidity (Figure 2) or by increasing the size of side chains to obstruct molecular motion. Modifying the primary chains serves to increase heat resistance. These techniques are used without exception to enhance the performance of engineering plastics (Tables 2 and 3).
Table 3 Examples of molecular chains and heat resistance
The strategy of enlarging side chains to increase rigidity is relatively easy to implement and is thus used to diversify the properties of general-purpose plastics. However, this approach does not affect the structure of primary chains, and thus yields minimal improvement in heat resistance.
The other approach—strengthening intermolecular forces—is intended to prevent neighboring molecules from separating, and includes strategies such as crystallization to yield ordered configurations, techniques for optimizing molecular structures, and efforts to increase intermolecular affinities.
Column 2: Crystallinity
As a chain-shaped molecule elongates, it adopts a zigzag configuration like that shown in Figure 3. When a molecule in such a state approaches another molecule, the molecules gradually settle into a state of maximal stability at a certain fixed intermolecular distance. As this process repeats, the elongated chains eventually form a configuration consisting of periodic arrays of regularly-spaced molecules (Figure 3)—that is, they form a crystal. Crystals are more stable and more dense than non-crystalline states of matter, and their strong intermolecular forces ensure high heat resistance and good mechanical properties.
The only polymers capable of forming crystals are those with molecular structures allowing easy alignment into arrays; plastics formed from such materials are known as crystalline plastics. In contrast, plastics that do not form crystals are known as non-crystalline plastics.
Figure 3: Intermolecular configurations in polymer materials
Column 3: Copolymers and polymer alloys
One widely-used technique is to blend plastic X with plastic Y to yield a new material with properties intermediate between the two component substances; as shown in Figure 4, there are two main ways to do this. The first approach, known as copolymerization, is to blend components X and Y at the sub-molecular level, yielding products known as copolymers. Polymers containing only a single molecular-chain component are known as homopolymers.
The second approach begins by separately forming molecules of substance X and molecules of substance Y, then blending the two types of molecules to yield a polymer alloy—a term borrowed from metallurgy to emphasize the analogy with metal alloys.
Figure 4: Copolymers and polymer alloys
Source: Isao Sato, ABCs of plastics(Japan Industrial Publishing Co., Ltd., 2011) (in Japanese)
(Written by Isao Sato, Isao Sato Technical Office)
Asahi Kasei is dedicated to providing a full-fledged grade lineup of engineering-plastic products—and to exploiting our unique technological expertise to improve product performance. Please contact us to ask any questions, discuss any concerns, and request samples.
Please contact us to ask any questions, discuss any concerns, and request samples.