- TOP
- Basic knowledge engineering plastics
- What are polyacetal resins (POM resins)?
What are polyacetal resins (POM resins)?
An overview of polyacetal resins: key properties and methods for molding and processing
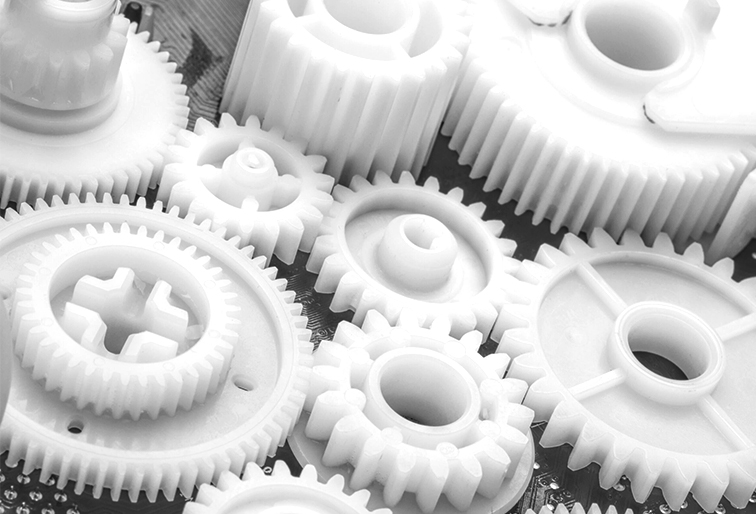
1.What are polyacetal resins (POM resins)?
Polyacetal resins (POM resins) are a family of engineering plastics whose chemical structures consist of ordered arrays of atoms in which methyl groups (CH2) alternate with oxygen atoms (O) (Figure 1). Due to the regularity of their chemical composition, polyacetal resins readily form crystal structures and exhibit the highest crystallinity of all engineering plastics. (The crystallinity of a resin is the fraction of its volume occupied by crystalline regions.)
Figure 1: Chemical structure of polyacetal.
The specific gravity of POM is around 1.4 g/cm3, which is relatively high compared to other general-purpose engineering plastics; this is due to the short distances between molecules in the crystal structure, yielding strength and stability. This high crystallinity is responsible for many of the key properties of POM. POM also has high latent heat of crystallization, a measure of the quantity of heat required to crystallize a material from a molten state; this fact has ramifications for the behavior of POM resins during the molding process.
In the absence of colorant additives, molded products made from POM are milky-white in color. This is due to crystal-domain structure: Molded bodies of POM incorporate both high-density crystalline regions and low-density non-crystalline regions, with light propagating through the two types of region at different speeds; this results in diffraction or reflection of light at boundaries between crystalline and non-crystalline regions, yielding an overall white appearance. This may be considered a common property of all crystalline resins.
2.Properties of polyacetal resins (POM resins)
The high crystallinity of POM resins gives these materials excellent mechanical properties, including strength and rigidity. In addition, the crystal structure tends to restrict molecules from shifting in position relative to each other, ensuring a high elastic recovery rate and giving POM high marks in the performance categories required for mechanical components—including resistance to repetition fatigue (material failure induced by repeated stress, even at low levels) and creep (a phenomenon in which materials subjected to stress for long periods of time exhibit significant shape distortion). Moreover, molecules embedded in crystal structures do not migrate when brought into close contact with other materials, making POM resins resistant to abrasion.
POM has an extremely low glass-transition temperature of -50°C; at typical working temperatures, the motion of molecular chains in non-crystalline regions of POM bodies yields a rubber-like consistency that is robust and rupture-resistant.
In general, it is difficult for organic-solvent molecules to penetrate into the interior of crystalline materials. For this reason, the high crystallinity of POM resins makes them highly resistant to organic solvents. On the other hand, POM exhibits no resistance to acids and only weak resistance to alkalis, so caution is required when using POM with inorganic substances. A further complication is that, once POM begins to decompose, the decomposition products exhibit their own chemical activity and serve to promote further decomposition. The decomposition of POM is promoted not only by heat, but also particularly by infrared radiation. For this reason, for products intended to be used outdoors it is important to select POM grades that have been subjected to weather-proofing treatment.
3.Varieties of polyacetal resins (POM resins)—and how to select among them
3-1. Homopolymers and copolymers
(1) Differences in molecular-chain structure
Because pure polyacetal chains are chemically unstable, they must be modified by the addition of stabilizing regions (stabilizing groups) to yield practically useful materials. There are two ways of doing this.
The first approach, illustrated in Figure 2-1, is to add stabilizing groups (denoted by X in the figure) to the ends of polyacetal molecular chains. This yields molecular chains that—aside from the stabilizing groups at their ends—consist exclusively of acetal structures, and the resulting material is thus known as homopolymer. The alternative approach is to blend substances providing stabilizing groups with other raw ingredients before polymerization; as illustrated in Figure 2-2 (stabilizing groups denoted by Y in the figure), this yields molecular chains that incorporate stabilizing groups in their interiors, not just at their ends. The material produced in this way, known as copolymer, contains a greater abundance of stabilizing groups compared to homopolymer.
Figure 2: Stabilizing groups in molecular structures of homopolymers (top) and copolymers (bottom)
In addition to preventing material degradation, stabilizing groups also serve to delay crystallization and decrease the melting point; these phenomena are related to the different material properties of homopolymers and copolymers, as summarized in Table 1. In practice, the choice of homopolymer vs. copolymer material is often determined by the nature of the application in question.
Table 1: Comparison of key properties of homopolymer and copolymer materials.
(2) Differences between homopolymers and copolymers
Homopolymer materials are easily crystallized, and molded bodies formed from homopolymers tend to exhibit high crystallinity, resulting in higher melting points and greater strength and elasticity compared to copolymers. One consequence of these properties is the outstanding creep resistance and fatigue resistance of homopolymer materials. On the other hand, copolymers are distinguished by their excellent environmental properties; compared to homopolymers, copolymers exhibit superior resistance to degradation caused by inorganic compounds (including acids and alkalis), heat, air, infrared radiation, and other factors.
3-2. Molten viscosity
The material properties of polymers are directly related to the length of the molecular chains they contain: in general, longer molecular chains yield greater resistance to creep and fatigue, but also higher viscosity in the molten state, which makes materials more difficult to mold into desired shapes. To offer our customers a wide range of options balancing performance and molding behavior, Asahi Kasei develops and sells a full spectrum of material grades featuring molecular chains of different lengths. As the overwhelming majority of POM products are produced by injection molding, material grades optimized for this purpose constitute the core of our lineup; low-viscosity (high-fluidity) grades featuring shorter molecular chains are typically used for miniature injection-molded components, while high-viscosity grades with longer molecular chains are used for extrusion-molded components or components requiring high mechanical strength or endurance.
3-3. Strength-reinforced grades
The strength and rigidity of plastics may be enhanced by adding reinforcing agents such as glass fibers or inorganic microparticles. Although it is difficult to preserve the affinity of POM for such reinforcing agents—and thus the strength-reinforcing impact of reinforcing additives is not as significant for POM as it is for other polyamide resins—Asahi Kasei nonetheless offers a wide range of grades boasting improvements in dimensional stability, electrical conductivity, and other properties.
3-4. Weather-resistant grades
In general, for products intended for use in outdoor environments, Asahi Kasei offers material grades treated with weather-proofing additives. In some cases, specialized grades—in which the types and volumes of these additives are optimized for specific usage environments—may also be developed. Due to the broad variety of reactivity properties exhibited by weather-proofing additives, weather-resistant grades may behave differently in different usage environments; thus, one must carefully verify that selected material grades perform as expected in their intended usage environments and exhibit no other performance problems.
3-5.Lubricating grades
Because POM is a common material choice for gears, slides, axle mounts, and other components intended for use with moving parts, Asahi Kasei develops and sells material grades with enhanced lubricating properties. Due to the wide variety of sliding motions and usage conditions to which components may be subjected, it may not be easy to identify the optimal material for a given application; we recommend carefully investigating a range of options—and testing materials under conditions that closely mimic actual operating environments—before making final selections.
3-6. Molding properties of POM materials
Components formed from POM are often subject to both stringent limits on dimensional precision and exacting requirements for functional performance; such cases require careful attention to the following characteristic molding properties of POM materials.
(1) The physical properties of POM materials may degrade when held for long times in high-temperature cylinders.
(2) Under certain molding conditions, the degradation of POM materials in molds may yield degradation products that contaminate the molds.
(3) Due to their high crystallinity, POM materials exhibit a high rate of shrinkage during molding.
(4) Due to their high latent heat of crystallization, POM materials are both difficult to melt and difficult to solidify.
Properties (1) and (2), which are common to all POM materials, may be addressed by blending with various ingredients, but still require careful attention during the molding process. Property (3) derives from the same crystallinity properties responsible for the high performance of POM—and is thus intrinsically unavoidable. Property (4), which is also related to crystallinity, requires that heat be supplied in sufficient quantities for melting and removed in sufficient quantities for solidification. Asahi Kasei also offers high-cycle grades of POM; these are subjected to a treatment that accelerates the onset of crystallization during solidification, allowing a reduction in cooling times.
4. Applications of polyacetal resins (POM resins)
Many applications of POM are designed to take advantage of the high strength and rigidity of POM materials, as well as their superior sliding properties; familiar examples from everyday life include garment zippers (Figure 3) and luggage accessories (Figure 4). These examples also illustrate how the spring-like behavior of POM materials is commonly exploited in practical settings.
Figures 3/4: Common applications of POM materials include garment zippers (left) and luggage accessories (right).
POM is also a common choice of material for moving components in electrical systems, including switch slides, gears, and cams. In industrial applications, fasteners made from POM can replace metal screws and bolts to help streamline assembly processes. Because POM materials exhibit excellent sliding behavior with no need for lubrication, they are an ideal choice for moving components operating in close proximity to electromagnetic systems or optical pathways, where the risk of contamination forbids the use of lubricants.
POM-fabricated moving parts are also used in precision instruments such as disk drives and paper-feed mechanisms, where they help reduce operating noise and avoid contamination caused by lubricating oils.
POM is a common choice of material for automotive components, particularly moving parts such as motor gears, door systems, mirror bases, head rests, and seat adjusters. Door handles are one example of an interior component that is monolithically integrated with a moving part—and for which an attractive appearance is thus essential. The excellent resistance of POM to organic solvents also makes it an ideal material for fuel-system components.
In the construction industry, POM is used for sash components such as sliding-door wheels, curtain-rail components, and water-supply valves. Similarly, in general machinery POM is widely used as a material for force-transmission systems and various types of sliding components and binders.
5.Methods for molding and processing polyacetal resins (POM resins)
Injection molding is the most common technique for manufacturing POM components. Two key prerequisites for successful injection molding are (1) accounting for the likelihood of significant shrinkage during molding, and (2) ensure that molding proceeds under appropriate conditions.
The high crystallinity of POM materials ensures a relatively high rate of shrinkage during molding: around 2%. Because precise shrinkage rates depend on molding conditions, products demanding high dimensional precision must be molded under carefully tuned conditions—and in properly configured molds.
One key parameter that must be carefully tuned is the temperature to which molten resin is heated during the molding process: setting this temperature too high may cause thermal degradation of the material, while setting it too low may prevent the resin from fully melting, degrading the quality of the molded products. It is also important that molds be thoroughly degassed; inadequate venting of gases from molds can not only cause short shots, but may also induce material degradation.
In addition to injection molding, raw POM may also be provided in the form of rods for cutting or slabs for extrusion molding. Due to the significant change in volume accompanying POM crystallization, when forming solid components one must take care to supply adequate volumes of molten resin to avoid the formation of voids. The low molten viscosity of POM makes it unsuitable for some molding methods, including blow molding and vacuum molding.
After molding, POM components may be subjected to a variety of secondary treatments; for some processes, including painting, printing, plating, and adhesive bonding, a surface-activation step may be required for good performance. For products made from POM components, a variety of assembly techniques are available, including screw junctions, snap-to-fit junctions, and welded junctions.
6. Polyacetal resins (POM resins) and global warming
The challenge of global warming is an increasingly dire problem affecting all mankind. Compared to general-purpose plastics, POM is used in relatively small volumes around the world and is rarely used to make single-use plastics—and, consequently, is rarely mentioned in discussions of Earth's environment. However, of all the various forms of plastic in use today, POM boasts an unusually minimal environmental footprint—and one which may be possible to reduce even further in future years.
6-1. Carbon usage
As noted above, POM may be described by the chemical formula (CH2O)n, from which a simple calculation yields a carbon ratio of 40%—an extremely small value compared to other plastic materials. For example, polyethylene, an typical example of a general-purpose plastic, has a carbon ratio of 85%, more than twice that of POM. This means that POM materials—at every stage of the product lifecycle, from manufacturing to discarding—have categorically smaller environmental footprints than other types of plastics.
6-2. POM production from biomass ingredients
POM is manufactured by industrial processes like that shown in Figure 5. Methanol, an intermediate ingredient in this process, is most commonly produced by oxidization of methane derived from natural gas. However, it is also possible to produce methanol by fermentation of biomass.
In this connection it is relevant to note that methane, the precursor from which methanol is produced, is a gas with greenhouse effects even more significant than those of CO2; methane is produced by the raising of livestock, emitted from lakes, marshes, and rice paddies, and generated by sewage-treatment plants. For these reasons, protocols for restricting emissions and ensuring efficient utilization of methane—following similar provisions for CO2—are a focus of active current research, and the use of POM for effective methane management offers one promising avenue toward a future freed from dependence on fossil fuels.
Figure 5: Production of polyacetal
→Click here to learn more about biomass-certified grades of Asahi Kasei's TENAC™ POM resins
Column: Crystal nuclei
When crystalline resins are in the molten state, their molecular chains exhibit active molecular motion and move freely around each other. As the temperature falls below the melting point, these chains settle into elongated configurations and begin to form crystals with neighboring molecular chains. These crystals then continue grow by incorporating nearby molecular chains, promoting solidification of the material.
The nature of this mechanism ensures that the rapidity of cooling-induced solidification is affected by the initial onset of crystallization; substances that promote this process are known as crystal nuclei. Crystal nuclei are solid bodies whose surfaces mimic the elongated structures of molecular chains; their function is to stimulate crystallization by incorporating nearby molecular chains, as illustrated schematically in Figure 6. The addition of crystal nuclei has the following consequences for the process of resin solidification:
• crystallization begins at higher temperatures
• the number of crystals increases
• crystallization proceeds more rapidly
• the solidified substance has higher crystallinity
• molded bodies contain fewer internal defects.
Crystal nuclei are used in the molding of POM products to shorten cooling times and reduce the number of residual defects in molded items.
Figure 6: Schematic depiction of role of crystal nuclei in stimulating crystallization.
(Written by Isao Sato, Isao Sato Technical Office)
Asahi Kasei is dedicated to providing a full-fledged grade lineup of engineering-plastic products—and to exploiting our unique technological expertise to improve product performance. Please contact us to ask any questions, discuss any concerns, and request samples.
Please contact us to ask any questions, discuss any concerns, and request samples.