- TOP
- Basic knowledge engineering plastics
- What are polycarbonates (PCs)?
What are polycarbonates (PCs)?
An overview of polycarbonates (PCs): key properties and common applications
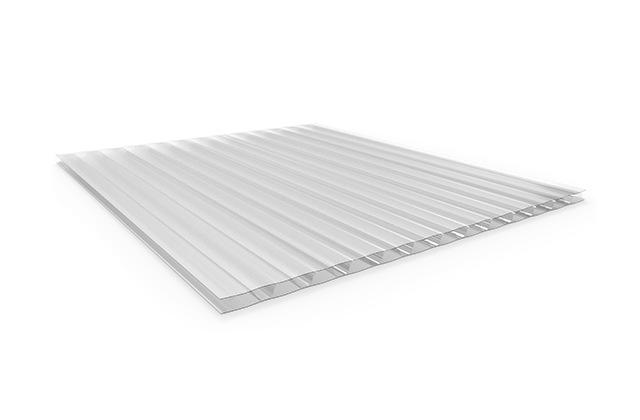
1.What are polycarbonates (PCs)?
Polycarbonates (PCs) are a family of non-crystalline general-purpose engineering plastics—and the only transparent materials among the various types of general-purpose engineering plastics. PC resins is a collective term used to refer to polymers in which monomers are chained together by carbonate groups through links known as carbonate ester bonds. The excellent impact resistance, transparency, heat resistance (high glass-transition temperatures around Tg ~ 150°C), and dimensional stability of polycarbonates make them a good choice of material for a wide range of applications. On the other hand, the ester bonds in polycarbonates make them less chemical-resistant than other materials (with particular susceptibility to alkalis and aromatic hydrocarbon-based solvents such as oils), and polycarbonates are also vulnerable to hydrolysis in warm, humid environments.
2.Production of polycarbonates
The basic chemical structure of polycarbonates is shown in Figure 1.
Figure 1: Chemical structure of polycarbonates
As shown in Figure 2, the unit depicted in Figure 1 is comprised of 4 molecular components: two phenols (red dashed lines), one acetone (green dashed line), and one carbonate (blue dashed line).
Figure 2: Molecular constituents of polycarbonate
The term polycarbonate derives from the presence of carbonate in Figure 2. More specifically, polycarbonates are materials consisting of polymer chains formed through repeated reactions of dihydroxy compounds with carbonate molecules, as shown in Figure 3.
Figure 3: Reaction that produces polycarbonates.
Varying the unit marked R in Figure 3 allows the creation of various distinct polycarbonates; the R unit chosen for industrial production is bisphenol A (BPA). As shown in Figure 4, BPA consists of two phenol molecules connected by an acetone molecule and is a common ingredient in products such as paints and adhesives.
Figure 4: Bisphenol A
There are multiple techniques for manufacturing polycarbonates, distinguished by the substance with which BPA is reacted. These methods are described in the table below.
Interfacial approach (interfacial polymerization) | BPA and phosgene are blended, reacted, and polymerized in the presence of catalysts. This method allows easy tuning of molecular masses and yields polycarbonates of excellent transparency. |
---|---|
Catalytic approach (ester-exchange process) | BPA and diphenyl carbonate (DPC) are blended, reacted, and polymerized in the presence of catalysts. |
Asahi Kasei's non-phosgene process | BPA is reacted with DPC—made from CO2 and ethylene oxide (EO)—and polymerized. Advantages include the use of CO2 as an ingredient and the non-use of phosgene, a highly toxic gas, as an ingredient. Note that Asahi Kasei does not manufacture PC itself, but rather licenses this technology to PC producers around the world. https://www.asahi-kasei.co.jp/tlb/en/index.html |
3.Features of polycarbonates
・Transparency:
Among all general-purpose engineering plastics, polycarbonates are the only transparent resins. Typical transparent material grades offer visible-light transmissitivies of 85-90% (for a 2 mm thickness of material).
• Impact resistance:
Of all plastics, polycarbonates offer the highest levels of impact resistance.
• Heat resistance:
With glass transition temperatures near 150°C, polycarbonates offer stable mechanical properties over a wide range of temperatures. Typical heat deflection temperatures—for general, non-strength-reinforced material grades—are around 120-130°C under heavy loading of 1.80 MPa.
• Dimensional stability:
Because polycarbonates are non-crystalline resins, they exhibit minimal shrinkage during molding and minimal dimensional variation under water absorption.
• Self-extinguishing properties:
Typical polycarbonate grades offer high flame retardance at the UL 94 V-2 level. Flame-retardant additives may also be added for applications demanding higher levels of flame retardance.
• Polycarbonates are susceptible to the influence of alkalis and aromatic hydrocarbon-based solvents such as oils.
• The ester bonds in polycarbonates make them vulnerable to hydrolysis in warm, humid environments.
Among the most attractive features of polycarbonates are their transparency and their good mechanical properties, particularly their excellent impact resistance. Polycarbonates also offer high dimensional precision, as their non-crystalline structure ensures minimal shrinkage during molding.
4.Applications of polycarbonates
Considered by volume of material used, the primary applications of polycarbonates are to electrical and electronic devices, office equipment, films and sheet materials, and automotive parts.
For electrical/electronic devices and office equipment, demand for LED illumination materials has grown significantly in recent years. The excellent optical transparency and heat resistance of polycarbonates makes them an ideal material for lenses. In electrical appliances for home and office, alloy materials blending polycarbonates with ABS are widely used as instrument chassis and case materials. Among the reasons for adopting polycarbonates are their good molding properties, the ease with which they can be colorized, their flame retardance, and their impact resistance.
In building construction and civil engineering, the high transparency and excellent impact resistance of polycarbonates makes them a widely-used choice of material for films and sheets. Liquid-crystal display panels is another high-volume application of polycarbonates.
In the automotive sector, perhaps the most prominent application of polycarbonates is to vehicle headlights (Figure 5). Modern light sources, advances in thermal design, the development of surface-hardening techniques, and other factors have led to the use of polycarbonates in most new vehicles, where they also help to reduce overall weight. Polycarbonates are also used for other transparent components such as instrument panels and various types of lenses—and for exterior components such as grills, as well as interior and structural components such as buttons and switches.
Beyond the applications mentioned above, DVDs and other optical discs (Figure 5) are also made from polycarbonates; the excellent transparency and heat resistance of PC resins make them an ideal material for this application, but the increasing prevalence of internet-based content distribution has led to declining demand.
Figure 5: Common applications of polycarbonates include vehicle headlights (left) and optical disks (right)
5.Polycarbonates and modified PPE resins: A comparison of key features and major applications
In addition to polycarbonates, the category of non-crystalline engineering plastics also includes modified PPE resins. In this section we briefly compare the key features of these two material families and describe the different ways in which they are used.
Polycarbonate | Modified PPE | |
---|---|---|
Specific gravity / weight reduction | ++++ | +++++ |
Low water absorption | ++++ | +++++ |
Hydrolysis resistance | +++ | +++++ |
Flame resistance | +++++ (depending on grade) | |
Molding properties | +++++ (depending on grade) | |
Electrical properties | ++++ | +++++ |
Heat resistance | +++++ (depending on grade) | |
Optical properties | Transparency | Non-transparency |
Colorization / discoloration | May be colorized | May be colorized, but yellow discoloration may ensue |
Impact resistance | +++++ | +++ |
Acid / alkali resistance | +++ | +++++ |
Resistance to organic solvents | ++ | ++ |
Table: Properties of polycarbonates and modified PPE resins
Applications of polycarbonates
Because polycarbonates are transparent and can be colorized, they are widely used for optical components and components affecting the external appearance of products. Polycarbonates are particularly ideal for applications demanding both transparency and high impact resistance, and are commonly used for automotive components and optical components requiring high heat resistance.
Applications of modified PPE resins
Modified PPE resins are used in a variety of applications exploiting their advantageous properties, which include low specific gravity (useful for weight reduction), hydrolysis resistance, chemical resistance, good electrical behavior, and high dimensional precision. Examples of such applications include peripheral components of lithium-ion battery systems, connectors for solar-power generators, products needed for 5G communication systems, and other applications which—though perhaps not prominently visible in everyday life—are nonetheless ubiquitous in the modern world.
→ Click here for an overview of Asahi Kasei's XYRON™ family of modified PPE resins
6.Processing methods
Because polycarbonates are frequently used in fields demanding high dimensional precision and low shape distortion, methods for assisting the flow of material into molds for injection molding—and techniques for improving the transfer properties of the surfaces of molded bodies—are a focus of ongoing development efforts. One example is the technique of injection compression molding developed for optical disks; in this approach, the cavity is widened during material infill to allow molten resin to flow more easily, then restored to its original thickness to ensure high-precision surface transfer. Another example is the development of surface-hardening treatments for automotive components requiring high resistance to abrasion damage.
7.Practical considerations relevant to use of polycarbonates
The high molten viscosity of polycarbonates requires certain special provisions for molds and molding procedures, without which molded products may contain defects, shape distortions, or cracks.
The chemical resistance of polycarbonates, though relatively high among transparent materials, is ultimately limited by their non-crystalline structures and carbonate bonds, thus requiring careful tuning of molding conditions to minimize shape distortion. One must also take care to avoid adhesion of machine lubricants during processing stages and to select mold-releasing agents that guarantee minimal residual impact. Similarly, when using molded polycarbonate products one must be careful to select only sprays and cleaning products that avoid undesirable side effects.
8.Polycarbonates and environmental sustainability
As discussed in Section 2, Production of polycarbonates, Asahi Kasei has developed a practical non-phosgene process for manufacturing polycarbonate using CO2 and EO as ingredients. This process, which makes no use of the highly toxic gas phosgene or the suspected carcinogen methylene chloride, is designed to prioritize safety, and its technology has been licensed to PC producers around the world.
Asahi Kasei also offers polycarbonate grades based on mass-balance methods for biomass compatibility. Although BPA, an ingredient used to make polycarbonate, is produced from phenol, these methods use substances derived from biomass ingredients for this phenol.
The primary method for recycling polycarbonate is material recycling, in which used resin material is ground into powder form, melted, and remolded. This approach is particularly useful for items such as used optical disks, which tend to be of high quality and are relatively easy to aggregate in large numbers.
Column: Melting phenomena in crystalline and non-crystalline plastics
When a non-crystalline plastic material is melted by heating above a certain temperature, neighboring molecules inside the plastic become free to move throughout the material. The temperature at which this occurs is known as the glass-transition temperature and denoted by the symbol Tg; at temperatures above Tg, the material begins to exhibit fluidity. The glass-transition temperature of polycarbonate is Tg~150°C.
The melting of crystalline plastics is slightly more complicated. A glance at the microscopic structure of crystalline plastics reveals the presence of non-crystalline regions coexisting with crystalline regions; at higher temperatures, the molecules in non-crystalline regions are the first to begin moving—while crystalline regions, in which molecules are bound by strong intermolecular forces and remain unable to move, continue to exist in the solid state. As the temperature increases further, molecules in crystalline regions begin to move freely as well, and the material begins to exhibit fluidity. The temperature at which molecules in non-crystalline regions begin to move freely is known as the glass-transition temperature (Tg)—the same term used for non-crystalline plastics. In contrast, the temperature at which molecules in crystalline regions begin to move freely is known as the melting point and denoted Tm.
Crystalline plastics at temperatures below Tg are said to exist in a glassy state, while between Tg and Tm one speaks of a rubbery state. Although both glassy and rubbery plastics are solids, their properties differ significantly: molecular behavior in the former state is reminiscent of the familiar properties of glass in daily life, while behavior in the latter state reminds one of the behavior of rubber, thus explaining the choice of terminology. Needless to say, for non-crystalline plastics there is no analog of the rubbery state. The relationship between temperature and plasticity state is depicted graphically in Figure 7.
Figure 6: Melting point and glass transition temperature
Figure 7: Relation between temperature and plasticity state.
(Written by Isao Sato, Isao Sato Technical Office)
Delivering engineering plastics industry news all at once! Introducing “engineering plastics Plastic Topics”
Asahi Kasei is dedicated to providing a full-fledged grade lineup of engineering-plastic products—and to exploiting our unique technological expertise to improve product performance. Please contact us to ask any questions, discuss any concerns, and request samples.
Please contact us to ask any questions, discuss any concerns, and request samples.