- TOP
- Basic knowledge engineering plastics
- What is the UL 94 standard?
What is the UL 94 standard?
We take a look at the flammability standard for plastics and the test methods used.
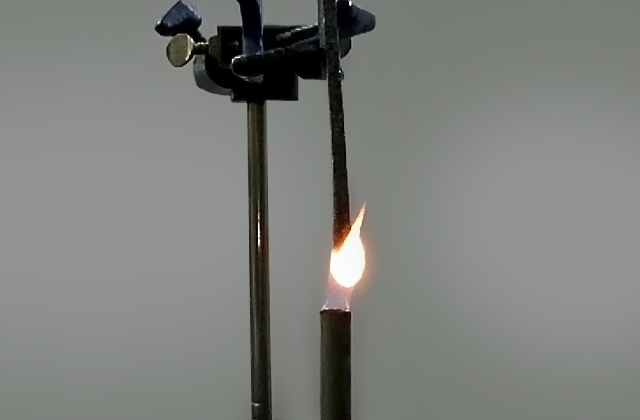
What is UL 94?
UL 94 is a safety standard for flammability testing of plastic materials for parts in electrical devices and appliances, certified by UL in the US. This page explains the features of UL 94 and the test methods used.
1. What does UL mean?
UL is an abbreviation of US product safety company UL Solutions, or the certifications issued by this company. UL Solutions is one of three organizations that make up UL Enterprises, which was formerly known as Underwriters Laboratories Inc. or Underwriters Laboratories Limited Liability Company (UL LLC). UL Solutions provides certification of materials, components, equipment, tools, and final products, with original standards and evaluation methods based on functionality and safety for each type of product. When a manufacturer submits an application, the product is evaluated according to the standard, and if it passes the evaluation, the product can be marked with the certification symbol.
UL standards certify that the results of testing the submitted specimens meet the standards that have been set; this does not guarantee the product. Products that have passed the test can be marked with the certification symbol, which helps users when selecting products. UL certification is widely trusted and supported because of the practical and appropriate test methods, robust and impartial operation, and follow-up such as unannounced inspections. For some types of products, the UL standards are treated almost as industry standards, and even influence national and international standards.
For plastics, the UL flammability standard in particular is globally recognized and is harmonized with many national and international standards. This is why the UL certification is often publicized for plastic products.
2. Features of UL 94
UL 94 testing involves actually burning test specimens using specified methods and rating the product depending on the results, such as how long it takes for the flame to go out. The specimen shape, conditions, ignition source, burning method, ratings according to burning status, and criteria are stipulated in detail in the published standard.
3. Burning test methods
3-1. Outline
UL94 includes the horizontal burning test (HB) which tests the rate of burning; the vertical burning test (V) which tests how long it takes for burning to stop; and the 5V test for applications that require particularly high flame retardancy, such as large products. Flammability is evaluated based on the burning time and burning rate.
3-2. Horizontal burning test
3-2-1. Test equipment
Figure 1 shows an outline of the test setup. One end of the specimen strip is attached horizontally to the stand, with the short side tilted at an angle of 45°. A 20-mesh wire gauze is placed below the specimen at a distance of 10 ± 1 mm from the specimen to catch any drips of molten plastic.
Figure 1. Horizontal burning test method
3-2-2. Test specimens
As shown in Figure 2, the test uses a specimen strip of width 13.0±0.5 mm, length 125±5 mm, and the required thickness (applications can be made for thicknesses up to 13 mm). Three specimens of each thickness are used. Before the test, specimens must be conditioned at 23±2°C, relative humidity 50±10% for a minimum of 48 hours. Lines are marked at 25±1 mm and 100±1 mm from the end to be ignited.
Figure 2. Shape of test specimen
3-2-3. Ignition source
The horizontal burning test uses a Bunsen burner of inner diameter 9.5 mm, with the flame length set to 20 mm.
3-2-4. Test method
The burner flame is applied to a position 6±1 mm from the edge of the specimen for 30 seconds and then removed. If burning reaches the 25 mm mark within 30 seconds, the flame is removed. After removing the flame, the time taken for the flame to reach the 100 mm mark from the 25 mm mark is measured to find the burning rate. If the flame does not reach the 100 mm mark, the combustion time and the distance from the 25 mm mark are measured.
3-2-5. Criteria
Materials that satisfy any of the criteria shown below are certified as UL 94HB.
Specimen thickness | Burning rate |
---|---|
Any thickness | Flame is extinguished before reaching 25 mm or 100 mm mark |
3.0 to 13 mm | ≤ 40 mm/min |
Less than 3.0 mm | ≤ 75 mm/min |
→Click here to see Asahi Kasei’s HB certified materials
3-3. Vertical burning test
3-3-1. Test equipment
The specimen is clamped at the top end to hold it vertically, as shown in Figure 3. A surgical cotton ball is placed at a distance of 300±10 mm from the end of the specimen.
Figure 3. Vertical burning test method
3-3-2. Test specimens
Five specimen strips for each thickness are used, of the same shape as the specimens for the horizontal burning test, as shown in Figure 2.
3-3-3. Ignition source
Like the horizontal burning test, the vertical burning test uses a Bunsen burner of inner diameter 9.5 mm, with the flame length set to 20 mm.
3-3-4. Test method
A flame is applied to the lower end of the specimen set up as shown in Figure 3. The flame is removed after 10 seconds. If the specimen stops burning within 30 seconds, the burner flame is immediately applied for a further 10 seconds. The following items relating to burning time, dripping, and position reached are recorded for five specimens.
- Burning time after first flame application
- Burning time after second flame application
- Burning and afterglow time after second flame application
- Whether combustion reaches the holding clamp
- Ignition of cotton balls by dripping of molten plastic
3-3-5. Criteria
Materials that satisfy the criteria below are certified as UL 94 V-0, UL 94 V-1, or UL94 V-2.
Item | UL 94 V-0 | UL 94 V-1 | UL 94 V-2 |
---|---|---|---|
Burning time for each specimen | ≤10 seconds | ≤30 seconds | |
Total burning time for 5 specimens | ≤50 seconds | ≤250 seconds | |
Afterglow time for each specimen | ≤30 seconds | ≤60 seconds | |
Burning upwards | Combustion does not reach holding clamp | ||
Ignition of cotton balls | None | Yes |
→Click here to see Asahi Kasei’s V-0 certified materials
→Click here to see Asahi Kasei’s V-1 certified materials
→Click here to see Asahi Kasei’s V-2 certified materials
3-4. The 5V test
3-4-1. Outline
The 5V test is a burning test performed on materials rated as V-0 or V-1. It consists of a vertical burning test with a specimen strip and a flat plate burning test.
3-4-2. Vertical burning test
- Test equipment:
The specimen strip is fixed vertically with a clamp, as shown in Figure 4, such that a flame can be applied at an angle of 20°. Surgical cotton is placed on the ground.
Figure 4. 5V vertical burning test
- Test specimens:The test uses specimen strips of the shape shown in Figure 2.
- Ignition source:The test uses a Bunsen burner of inner diameter 9.5 mm, with the flame length set to 125±10 mm and the blue flame length set to 40±2 mm.
- Test method:A flame is applied to the lower end of the specimen for five seconds, then removed for five seconds. This is repeated five times, and the burning of the specimen is observed and recorded.
3-4-3. Flat plate burning test
- Test equipment:A 150 mm square flat plate is fixed horizontally as shown in Figure 5, such that a flame at an angle of 20° can be applied to the center of the plate.
- Test specimens:This test uses a flat plate with dimensions of 150 mm × 150 mm.
- Ignition source:The flame length of the burner is set to 125±10 mm, the same as for the specimen strip test.
- Test method:A flame is applied below the center of the flat plate for five seconds, then removed for five seconds. This is repeated five times, and the burning of the specimen is observed and recorded.
Figure 5. 5V flat plate test
- Criteria:Base on the results of each test, materials that satisfy the criteria below are certified as 5VA or 5VB.
Property | 5VA | 5VB |
---|---|---|
Material used | Compliant with V-0 or V-1 | |
Vertical burning test | Burning + afterglow time after 5th flame application is ≤60 seconds | |
Cotton balls not ignited by drips | ||
Flat plate test | No holes formed | Holes formed |
→Click here to see Asahi Kasei’s 5VA certified materials
→Click here to see Asahi Kasei’s 5VB certified materials
Products certified according to the tests above:
- are assigned a registration code (ID)
- are permitted to display UL marking
- are issued a card (UL Yellow Card) showing the certification details.
Click here to search Asahi Kasei’s UL Yellow Card registered materials
As well as the UL standards, there are other industry-specific flammability tests for plastics.
One example is EN 45545 for the European railway industry. In railways and other public transport systems, a fire could break out in a tunnel or underground, where it would be difficult to safely evacuate passengers. In such cases, the spread of fire must be slowed down as much as possible to allow passengers to get out safely. This means fire safety requirements for the materials used needs to be more stringent.
EN 45545 specifies fire protection requirements for railway vehicles, taking various hazard levels into account, and is a European legal framework. First published in 2013, EN 45545 is now a mandatory requirement throughout Europe, and there are growing requirements for materials equivalent to this standard in Asia, too. EN 45545-2 is the part of EN 45545 that specifies requirements for materials and components. Products to be used in European railways are required to use materials compliant with EN 45545-2.
→Click here for resin materials compliant with European railway standard EN 45545-2
(Written by Isao Sato, Isao Sato Technical Office)
Delivering engineering plastics industry news all at once! Introducing “engineering plastics Plastic Topics”
Asahi Kasei engineering plastics The general information site provides monthly downloadable information and news on the engineering plastics industry and technology trends, carefully selected from a large number of overseas specialized newspapers. This is the popular content of our site.
Please contact us to ask any questions, discuss any concerns, and request samples.