- TOP
- Fundamentals of CAE
- Part 4 What is injection molding?
Series: Fundamentals of CAE Analysis for Plastic Product Design
Part 4 What is injection molding?
From the 4th to the 9th, we will sequentially introduce the injection molding simulation from the material data to be used to the specific application contents such as molding defect countermeasures.
In this article, we will focus on injection molding.
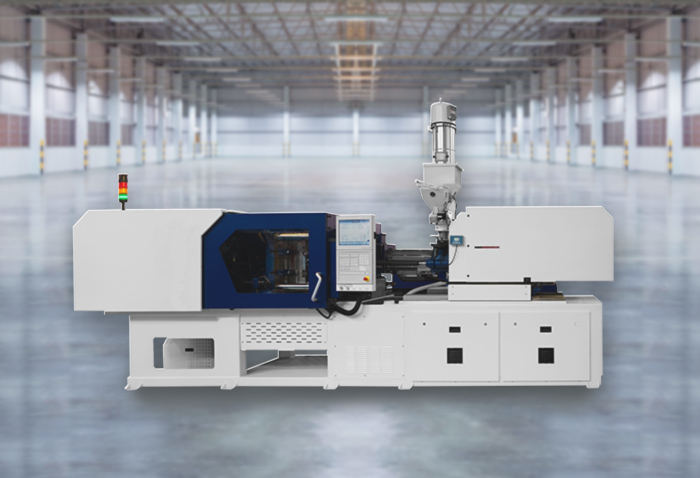
Contents
1. What is injection molding? |
2. Structure of mold for injection molding |
3. Special injection molding methods |
4. Other major molding methods |
5. Summary |
What is injection molding?
Injection molding is a method of molding 'thermoplastics' into desired shapes. Plastic materials are melted by heating, injected under pressure into a mold, and cooled to solidify the resin.
It is possible to mold complex shapes, enabling the production of a wide variety of products. In addition, the short molding time per part and the ease of automation of the entire process make it suitable for mass production.
Fig. 1 Example of horizontal injection molding machine
An injection molding machine consists of an injection unit and a mold clamping unit. First, in the injection unit, granular plastic raw materials (pellets) are fed from the hopper and melted by heating in the cylinder. The melted resin is extruded under high pressure with a screw and injected into the mold through a nozzle. In the mold clamping unit, after the mold is closed and the resin is injected, it is cooled and hardened. Then open the mold and take out the molded product. The injection molding cycle consists of mold clamping → injection → holding pressure → cooling → mold opening → ejecting. Holding pressure is a process in which the resin expands when heated and contracts when cooled, so the shrinkage is compensated for by applying pressure and feeding the resin further.
Structure of mold for injection molding
The mold for injection molding is shaped like a taiyaki mold. The side that opens when the mold is opened is called the movable side (core), and the side that does not move is called the fixed side (cavity).
Fig. 2 Movement when opening and closing the mold
The sprue is the part injected from the nozzle of the injection molding machine when you look at the molded product taken out of the mold. It has a conical shape so that it can be easily removed from the mold. Molten resin flows from the sprue through a flow channel called a runner, and flows into the product. The boundary between the runner and the product is called a gate, and various shapes are selected depending on the product. Plastic models are sold with the parts attached to the runner, but in normal products, the sprue and runner parts are unnecessary and must be removed. Also, the seam between the fixed side and the operating side is called a part line (PL).
Fig. 3 sprue, runner and gate of the molded product
■ Two plate mold
A mold that consists of a fixed side and a movable side. Since the number of parts is small and simple, the cost of the mold can be kept low, but since the molded product is discharged with sprues and runners still attached, a post-treatment called gate cutting (runner treatment) is required to remove these. is.
Fig. 4 Two-plate mold image
■ Three plate mold
This mold consists of three parts: the fixed side, the movable side, and the runner stripper plate. Since the sprue and runner are removed from the product when the mold is opened, it is suitable for automation.
Fig. 5 Three plate mold image
■ Hot runner mold
This is a mold that heats the sprue and runner parts with a heater and allows only the product part to be ejected. Not only does this eliminate the need to process runners and sprues after molding, but it also reduces waste of plastic raw materials, making it suitable for automation and mass production. The mold cost is high because the mold structure is complicated, including the built-in heater that heats the runner.
Fig. 6 Hot runner mold image
■ Gate type
There are various types of gate shapes, and optimal suitable one must be selected based on the product shape, application, molding method, etc. Here we will introduce some typical types.
・Direct Gate
Fig. 7 Example of direct gate
This is a method that flows directly from the sprue into the molded product without going through a runner. Suitable for large molded products, but post-processing is required as large gate marks remain. It is often used for molding things such as buckets.
・Side gate
Fig. 8 Side gate example
This is a method to attach a gate to the side of the product. It is often used because multiple molded products can be obtained and processing is easy. Since post-processing is required and gate traces remain, it is necessary to consider installing the gate in an inconspicuous place.
・Film Gate
Fig. 9 Film gate example
This method attaches a thin film-like elongated gate along the molded product. Since the gate width is wide and the resin flows evenly, it is suitable for thin plate-shaped molded products that are prone to deformation and distortion. It is also used to prevent molding defects due to the orientation of resins containing fillers such as reinforcing fibers. Since the gate is thin and wide, it is difficult to remove the gate marks and requires post-processing.
・Pin gate
Fig. 10 Pin gate example
Gates used in three plate molds. Suitable for automation because the gate breaks off when the mold opens and the part separates from the runner. You can set multiple gates or take multiple parts. In that case, it is necessary to consider the balance and determine the position so that the resin can be poured into each molded product at the same time. Since it is necessary to make the gate smaller, it may be difficult for resins with low fluidity or fillers.
・Submarine Gate
Fig. 11 Submarine gate example
This is similar to the side gate, but this is a method of pouring the resin as if it were crawling under the product. Also called tunnel gate. No post-processing is required as the gate breaks when the mold opens. As with pin gates, it can be difficult for resins with low fluidity or filled resins.
Special injection molding method
Currently, various special molding methods have been developed to solve problems and improve quality in injection molding. Here are some representative examples.
■ Gas injection
Gas injection (gas-assisted molding) is a holding pressure process in which pressure is applied until the product is cooled and solidified after being filled with resin in the normal injection molding process. Sink marks (dents that appear on the surface when the resin cools and shrinks) and warping of molded products can be suppressed, improving dimensional accuracy.
■ Supercritical foaming
When nitrogen or carbon dioxide is placed under high temperature and pressure conditions, it becomes a state in which both gas and liquid are present. A substance in this state is called a supercritical fluid. This is a molding method in which a supercritical fluid is injected into a resin as a foaming agent and melted, and then abrupt changes in pressure and temperature are applied to generate microscopic foams. As a result, the inside of the molded product becomes a microcellular structure. The effect of reducing the weight of molded products can be expected. In addition, since the fluidity is improved, it is possible to make the wall thinner and reduce the amount of resin used. Furthermore, by generating uniform air bubbles inside the resin, pressure is evenly applied, which can be expected to prevent warping and sink marks and improve dimensional accuracy. It reduces the mold clamping force of the molding machine and eliminates the need for holding pressure, making it possible to shorten the molding cycle.
■ Heat and cool
When molten resin is filled into a mold, if the mold temperature is low, the resin will cool rapidly and harden where it touches, resulting in appearance defects such as weld lines (grooves that form where the resin joins inside the mold). Therefore, the inside of the mold is heated with a heater or other device to ensure that the resin has optimal temperature to transfer the shape of the mold. Furthermore, by rapidly cooling the mold to harden the resin, this method can improve the appearance quality of the molded product, such as eliminating weld lines and flow marks.
Other major molding methods
In addition to injection molding, there are many other types of molding methods for thermoplastics. Some of the major molding methods are briefly described below.
■ Extrusion molding
This molding method is suitable for manufacturing tube-shaped products such as hoses and straws, as well as long products with uniform cross-sectional shapes such as rails and sashes. Molding is performed by extruding heated and melted resin from a mold (die) with a cross-sectional hole. The extruded resin is cooled by water or air to harden. Depending on the shape of the die, it is possible to continuously form pipes with various cross-sectional shapes.
■ Blow molding
This molding method is suitable for molding hollow shapes such as PET bottles. The melted resin is extruded into a cylindrical shape, set in a mold, and inflated like a balloon by injecting high-pressure air from the mouth. It is molded by pressing the resin against the mold from the inside with the power of air and making it adhere. Not suitable for molding complex shapes.
■ Vacuum forming
This is a method for molding egg cartons, packages for miscellaneous goods and foods. A sheet of resin is heated, softened, set in a mold, and air is sucked out to create a vacuum, which is then adhered to the mold for molding. Materials other than metal, such as gypsum and wood, that are easy to process can be used for molds, and can be molded at relatively low cost. Although it is possible to mold large objects such as automobile dashboards, bumpers, and bathtubs, it is not suitable for molding precise and complicated shapes.
Summary
In mass production design of plastic products, it is necessary to know the basics of mold structure and injection molding. This is because it is necessary to select molds and gate shapes that match the application and characteristics of the product. In the injection molding simulation, you can simulate the entire injection molding process and check the defect phenomena in the actual molding, which can be useful for designing the mold and setting the molding conditions. We will explain in detail how it can be used from the next part.
Next Part: "Let's learn about material data items used for injection molding simulation"
For more information about CAE, please contact us.
CAE Download Slides
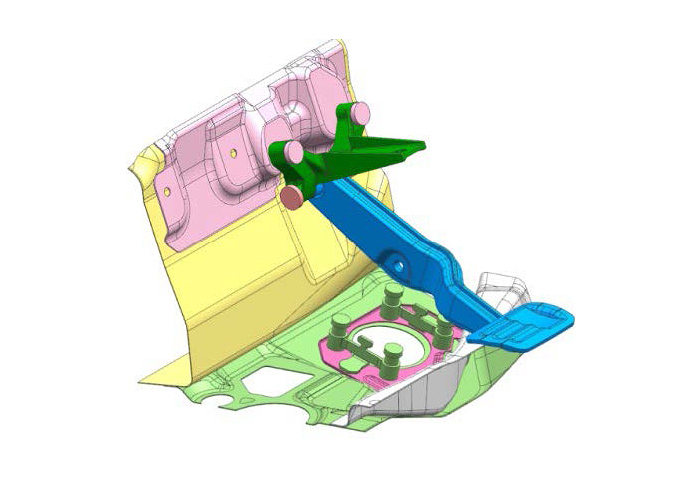
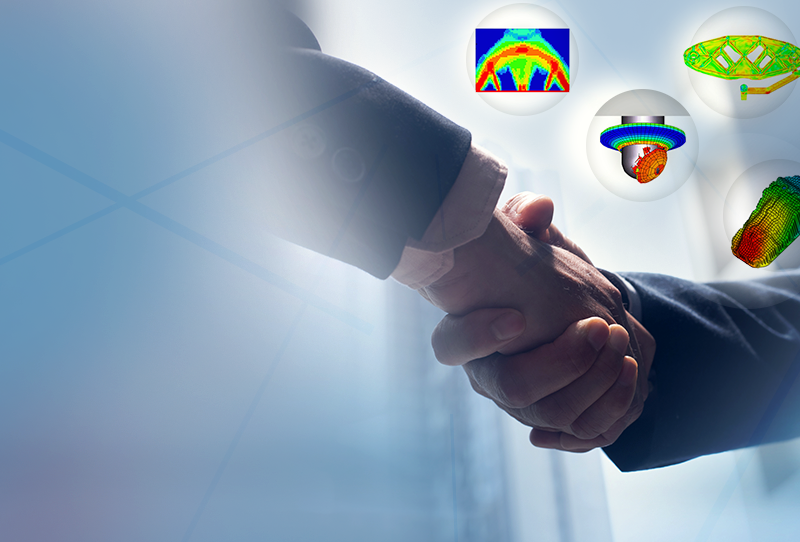