- TOP
- Sustainability
- Manufacture the product
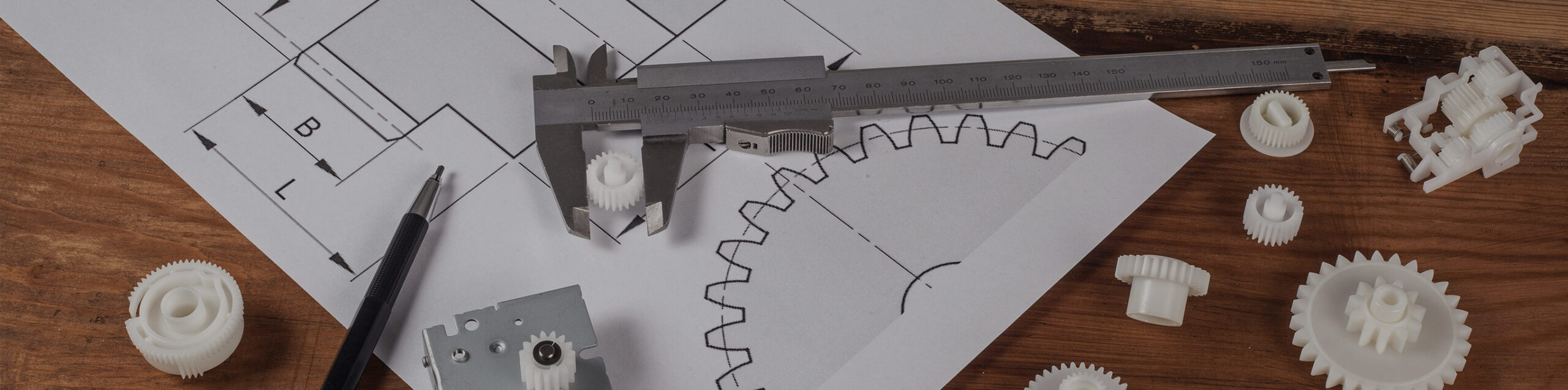
Sustainability
Producing products
Contents
Summary
- We will look at three approaches to achieving resource conservation when manufacturing products: 1. Reducing material usage, 2. Reducing processes, and 3. Reusing scrap materials.
- Shape optimal, multiple part integration, and product miniaturization can reduce the amount of material used. Here we introduce examples of optimal shape proposals using Plastics CAE Technology.
- By minimizing manufacturing processes such as assembly and painting, labor costs (human costs), processing energy, and material waste can be reduced. We will introduce materials that realize shapes that are easy to assemble and products that can reduce the painting process.
- Resin waste generated during the manufacturing process is crushed and a certain percentage is mixed into the product for reuse (regrinding), which reduces the total amount of resin used. We will introduce materials with excellent thermal stability and regrindability.
Reducing resource usage in product manufacturing
One strategy for manufacturing products in more environmentally-responsible ways is simply to reduce resource usage. This is not a new idea—indeed, some time ago it was enshrined as the first of three exhortations in the widely circulated slogan “reduce, reuse, recycle.” Below we discuss three strategies for reducing resource usage in product manufacturing.
Three strategies for reducing resource usage:
- Reduction in material usage: Reduction in product weight through shape optimal and miniaturization, reduction in material usage through fewer parts
- Process reduction: Reduction in the number of parts or elimination of assembly processes due to easy-to-assemble shapes, elimination of painting processes due to the use of materials with excellent appearances
- Recycling of scrap materials: Reusing scrap materials that would have been discarded up until now as regrind material reduces the amount of material used.
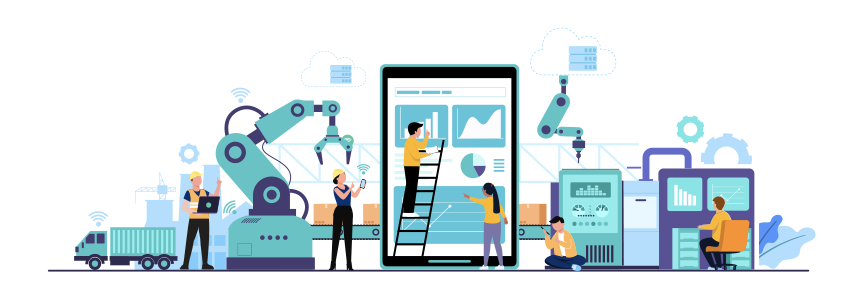
Reducing material volume and saving processing steps
The products we use in our daily lives—from household appliances to cars—are composed of many components, and they are produced via complicated processes involving many steps, from component molding to product assembly and painting.
Reducing the number of processing steps to the bare minimum can cut labor costs (personnel costs), save energy in post-processing steps, and minimize losses of constituent materials. Other ways to reduce resource usage in manufacturing include using smaller quantities of resins to produce each product, and saving paints.
(1) Reducing the volume of material used
A. Reducing the amount of resin used by reducing the number of parts and optimal the shape and weight
By optimizing the shape of products, it may be possible to reduce the number of components—for example, by adopting monolithic, integrated architectures to replace assemblies of multiple components—and to reduce the size and weight of products. Computer-aided engineering (CAE) for resin materials is a powerful tool for determining optimal shapes for product designs.
B. Use of paint-free materials
Choosing materials with weather-resistant and good surfaces, or materials capable of expressing metallic coloration without painting, can save painting steps from production processes and reduce use of plating materials and solvents. This also helps to advance the goal of item (2) below by saving processing steps.
(2) Saving processing steps
A. Easy-to-assemble design
Compared to metals, engineering plastics offer significantly greater shape flexibility, allowing product designs to be optimized for maximal ease of assembly. Products that are easy to assemble not only save assembly steps in production processes but may also obviate the need for certain screws and bolts, helping to reduce resource usage.
B. Use of materials with good formability that do not require post-processing
Some product-manufacturing processes require secondary processing steps, such as burr removal or annealing to repair warping or strain. Choosing materials with less susceptibility to warping or burr formation may save the need for such post-processing steps.
Reusing material wastes
The waste materials such as sprues and runners generated during the manufacturing process using resin are crushed by the manufacturer and recycled as molding material. Regrind material can generally be added at a certain ratio to new virgin material as long as the various performance properties are not reduced.
Making effective use of regrind—material that would otherwise be discarded—can help to reduce the total quantity of resin required to manufacture a given product.
Asahi Kasei’s Recommended Solutions (1)
Reducing component counts and saving process steps
SunForce™ modified PPE foam beads offer greater flexibility in designing products
SunForce™ combines the excellent properties that only foams can offer—light weight and thermal insulation—with flame retardance (UL-94 V-0), dimensional stability, and the ability to form products with thin walls. SunForce™ is a foam material offering functionality far beyond the capabilities of conventional foams. This material exhibits exceedingly small dimensional variations in processing and offers formability properties nearly equivalent to those of typical injection-molding materials, making them ideal for worry-free use in applications such as structural bodies and equipment chassis, where high dimensional stability is essential.
SunForce™ also features the unique strengths of PPE resins—specifically, low coefficients of linear expansion relative to other resin materials—and remain relatively unaffected by temperature fluctuations.
SunForce™ is produced by filling beads in tooling and applying steam to induce swelling in these beads, resulting in thermal bonding. Thus, in contrast to injection molding—in which resin is injected into a tooling at high temperature and high pressure—the SunForce™ process tends to produce minimal warping and few sink marks in finished products, even for products with spatially-varying wall thicknesses. This saves the need to impose shape constraints—such as uniform wall-thickness requirements—offering greater flexibility in designing products.
Exploiting this flexibility—for example, by fabricating molded products with shapes conforming to substrates or harnesses—may, in some cases, save the need for screws or bolts to fix components in place when assembling component packs, simplifying production processes.
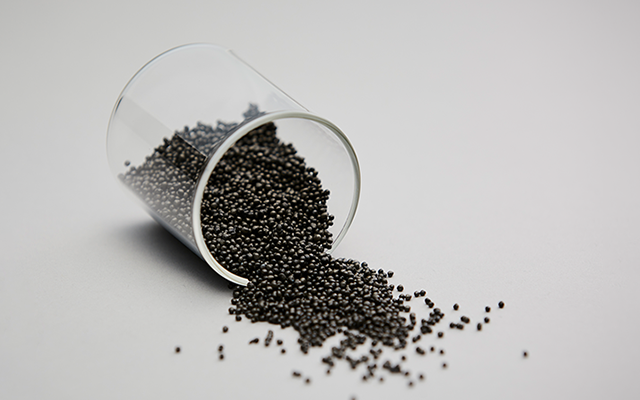
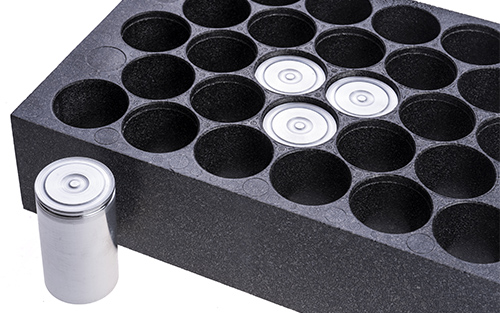
Metallic-colored POM materials save painting steps to cut costs and reduce environmental impact
Polyacetal (POM) features excellent mechanical properties, sliding behavior, and chemical resistance, and is used for many structural components and internal components.
Asahi Kasei’s TENAC™-C ZM413POM resins are metallic-colored POM copolymers with physical properties and weather resistance equivalent to those of standard weather-resistant grades. This material also complies with various automotive OEM regulations restricting the emission of volatile organic compounds (VOCs) for materials intended for use in automobile interiors.
Typical methods for imparting metallic finishes to products involve painting or plating on the surface of the base resin. However, such approaches are costly due to the multiple processing steps they require—and have the additional drawback of polluting the environment through the use of solvents at various stages. We recommend to choose TENAC™-C ZM413 which may save these drawbacks by omitting painting steps from your production process.

- Details on metallic-colored POM resin TENAC™-C ZM413 available here.
Weight reduction by replacing metal to plastic & optimizing parts design through the use of resin CAE
Asahi Kasei has "Plastics CAE Technology" an analysis technology specialized for resins.
The following is an example of how Plastics CAE Technology is being used.
The original product (far left image) wasmade of steel and consists of multiple components. We used
CAE technology to perform a topology-optimization analysis (intermediate images), resulting in a final design proposal in which the product was made from resin instead of steel (images at right) and achieved a weight reduction of more than 80% compared to the original design.
In this case, taking advantage of Asahi Kasei’s resin CAE technology allowed the designer to identify the most efficient distribution of materials within the established design space, subject to the structural limitations and loading and constraint conditions relevant for the scenarios in which the product was expected to be used.
Moreover, the shapes produced by topology-optimization analysis are extraordinarily flexible; in the case study depicted here, this freedom—together with the skill and experience of the engineer performing the analysis—produced an innovative injection-molding design featuring a totally novel shape unlike any existing design and, indeed, beyond the confines of any existing design paradigm. Further investigation revealed superfluous regions of the proposed design; saving these further simplified the shape of the product, ultimately succeeding in decreasing the number of components and dramatically reducing the weight of the final product.
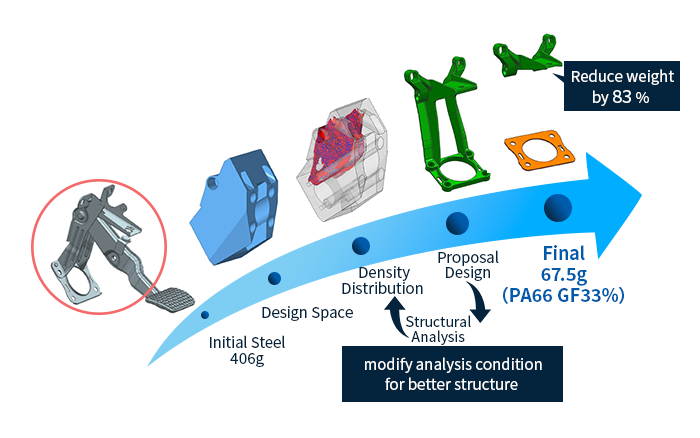
Case study: Replacing metal hinges with high-strength, good appearance polyamide that require no painting or plating
Hinges, used primarily for doors, must be high-strength components and are thus typically made of die-cast metal. However, making attractive hinges typically requires decoration via plating—a process that generates waste water containing metal ions, whose disposal entails heavy environmental impact.
Asahi Kasei’s LEONA™ SG series of polyamide resins not only satisfy all performance requirements demanded for hinges, but also yield attractive final products without painting or plating, slashing overall weight and reducing waste to lessen the environmental impact of the manufacturing process.
Case study: chassis for air-pressure regulators, replacing metal with high-strength polyamide saves post-processing steps and yields lighter-weight products, reducing shipping-related energy consumption
Air-pressure regulators are key components installed at many product-manufacturing sites. Because the chassis bodies in which these instruments are enclosed must have a high strength, they are typically made of metal. On the other hand, because the regulators incorporate networks of fine-grained flow pathways to control air flow, their production consumes significant quantities of energy and entails heavy material losses. Switching from metals to Asahi Kasei’s high-strength LEONA™ S series of resins saved the need for post-processing steps, helping to streamline production processes.
Also, because air-pressure regulators are shipped to customers around the world, the reduction in product weight achieved by replacing metals with resins significantly reduced shipping-related energy consumption.
Asahi Kasei’s Recommended Solutions (2)
Reusing product wastes
XYRON™ modified PPE resin are excellent for regrind
XYRON™ modified PPE resins are materials that offer excellent thermal stability and hydrolysis resistance, and exhibit minimal degradation in physical properties when used as regrind, making them easier to reuse than other resins. This material also boasts the lowest specific gravity of all engineering plastics; its light weight helps to reduce the volume of material used in manufacturing.
Exploiting these properties by using modified PPE resins to manufacture products—and reusing sprues, runners, and other wastes produced at manufacturing sites—allows you to reduce total material usage and minimize environmental impact.
Note: In cases where the external appearance of products is important, impurity contamination due to the use of reused materials can produce defects that result in unattractive products. Avoiding this situation requires carefully optimizing the percentage of reused material used; as a rough guideline, we recommend considering percentages of 20% or below.
We would like to talk to you about Asahi Kasei’s sustainability solutions. Please contact us to ask questions and request samples. We look forward to hearing from you!
Inquiries