Technical Information
Case studies-1
Gate position optimization
An oil pan of an automotive part was modeled, and the gate position was optimized to reduce warping deformation of the flange. Resin flowed along the flange to increase fiber orientation and improve rigidity. Comparison of the warp deformation obtained from the analysis with the actual warp deformation showed a close match.
For details, please see CAE Case Study "Accuracy Validation of Warpage Analysis".
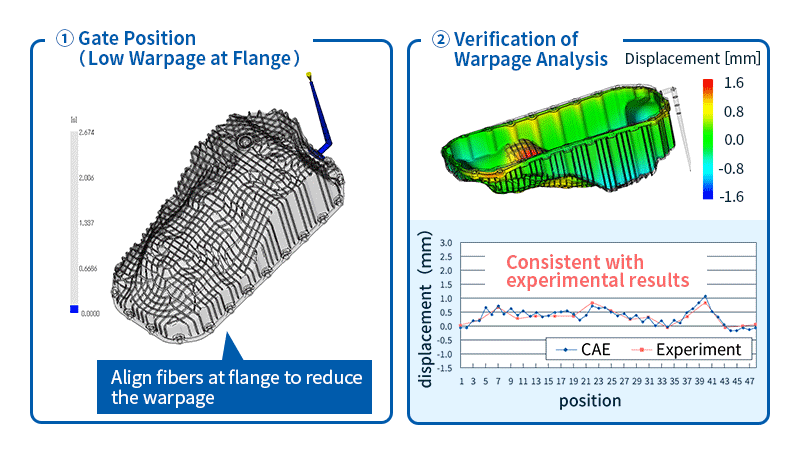